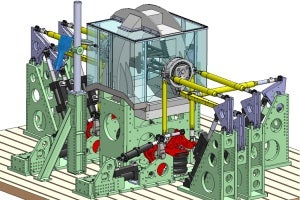
Increasing customer demands and stringent emission regulations require today’s vehicles to be more efficient than ever. Today’s customer demands for driving dynamics, comfort and safety require sophisticated and complex chassis systems. Specific targets for convenience, cost and weight make it necessary to verify the physical limits of chassis components, and special test benches for extensive testing of the chassis systems are therefore required.
In order to achieve more realistic test conditions, Magna Powertrain’s ECS improved the already-existing axle test bench. The adapted axle test bench includes a modular saltspray corrosion cabin and allows the steering movements of front axles to be tested under a variety of conditions.
This test bench provides very realistic conditions to investigate passenger car and light commercial vehicle axles (up to 2.5t axle load). The geometry of the force application components enables steering angles up to +/- 25°. Furthermore, steering angles up to +/-45° are possible for quasistatic analyses, such as functional tests. To simulate the wheel loads in six degrees of freedom, the forces are exerted on the wheel adapter (using lever systems) by 12 servo-hydraulic linear cylinders.
Servo-hydraulic devices and a CAN Bus-controlled electric servomotor both steer the angle application in real-time. Active steering systems may require a simulation of further CAN Bus or FlexRay signals for operation. Since different types of power-assisted steering systems are common, hydraulic or electric energy supply is provided. To realise a further load case on the specimens, an implementation of driving torque at the axle drive is possible.
As a result of the need for lightweight designs in the automotive industry, the use of aluminum parts is increasing. Since intergranular corrosion is common when aluminum is exposed to road salt (depending on the used alloy), the durability of such parts could be reduced by 30-50%. This factor must therefore be offset, usually by increasing the damage content of the load spectrum. If the influence of the corrosion cannot be evaluated or an adaption of the damage content is not desired, testing under salt spray atmosphere provides the best solution.
The challenge of this project was to combine the moveable wheel adapter and cabin. The cabin, in which specimens are coated with salt spray, encloses all chassis components which must be tested. As the wheel adapter is moving, a flexible interface is needed inside the stationary cabin. This was achieved by use of a special curtain, which was stretched on a frame to seal the cabin.
During the development process, many test bench components were newly designed or adapted. To ensure that the force applied to the components fulfilled the requirements of kinematics, free travel and strength, a multi-body-simulation (MBS) was performed. The behaviour of the real test bench was simulated and evaluated using ECS’s FEMFAT Lab Virtual Iteration. This software tool allowed the load data for MBS models to be determined.
In conclusion, Magna Powertrain’s ECS centre’s steered axle test bench with salt water corrosion features a unique combination of environmental simulation and fatigue testing. This has the advantage of more realistic test results and achievement of shorter development cycles for OEMs.