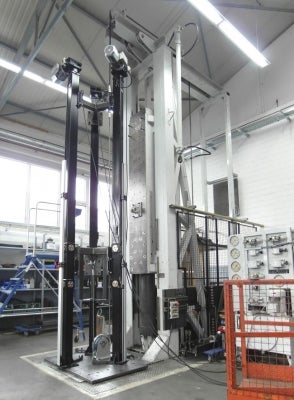
Customised work platforms with a high safety standard are used for the maintenance of modern aircraft fleets. The advantage of these is that they can be quickly adapted to the respective aircraft types.
haacon designed the required adjustment drives with synchronous control for a larger version of the Airbus ‘Beluga’ transport aircraft, and these drives were delivered to a French aeronautical system supplier.
Due to the dimensions available in the aircraft construction, individual modules with a weight of up to 4,500kg are grouped in larger units and mechanically or electrically coupled with each other depending on spatial conditions. The group can be subsequently synchronously height-adjusted.
The project required a stroke of 1,600mm at a speed of 520mm per minute. Limit position sensors monitor the maximum adjustment path. All adjustment drives installed in the group are synchronised in the master / slave principle. The drives used are characterised by a jerk-free soft start and soft stop, resulting in a high degree of operating comfort. Elastic contact strips with a switch-off function protect the aircraft fuselage against damage.
The control is equipped with an enabling button, and this comes with a second operator at a position that may not be visible to the main operator, is prompted to enable the adjustment. If one of the two operators interrupts the control contact then the adjustment movement is halted.
The electromechanical safety concept encompasses the self-locking effect of the spindle-nut package, an additional holding brake, minimisation of the guide tube play, and a safety nut. The safety nut performs load-free movement on the spindle in normal operation.
The load is held or adjusted by the so-called support nut. If a support nut should break, the load is transferred to the safety nut. This state is monitored by the control.