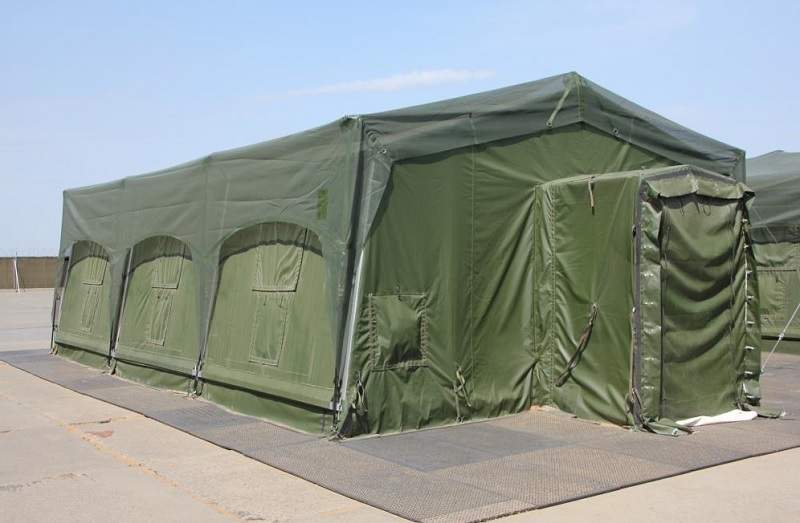
HTS TENTIQ is the Military and Humanitarian Division of the global temporary structure manufacturer HTS TENTIQ ; a family run business with the owner Mr Heinz Röder and his son Wilhelm Röder actively playing a part in its daily running.
The company focuses on quality and innovation through all products and divisions. This ethos at the heart of the company ensures all military and humanitarian products are setting the industry benchmark in terms of design, technology, materials, production and deployment.
Technology for the future
Although the roots of the company are well set in the past with the Röder family having more than 50 years of experience within the tent industry, the philosophy of the company is to look to the future and embrace new ideas and technology. The production facilities use state-of-the-art CNC machines to produce structures of the highest quality, enabling the company to offer a product range second to none within the industry.
Investment, development and innovation
Examples of this investment and development are shown in two completely separate areas within the company and the first is within the PVC cover factory.
Due to its volume of orders, HTS TENTIQ requires the mass production of PVC covers. The original factory setup was unable to keep up with the volume required so HTS TENTIQ decided to invest in new machinery. At first they looked at off-the-shelf solutions but were not convinced they offered a suitable solution. The answer was to develop and build a new machine unique for HTS TENTIQ, which could produce not only the volume of covers required at the time, but had a built-in capacity for the future. Today, HTS TENTIQ is the proud owner of a unique machine with a capacity to produce 100m run per hour of ready finished covers.
The second area of development was a brand new product that combined the known properties of an aluminium profile with the strength and flexibility of carbon fibre. The result is a stronger product so the profile size of the structure can be reduced, saving weight and volume in the overall structure. Alternatively, wind and snow loads can be increased using standard sizes. The product took more than four years of investment to develop and is protected by a world patent.
Quality Control
The company also realised at an early age that by concentrating on product quality and investing in Quality Control resources they could increase efficiency and sales by having the reputation of supplying the best quality product on the market. This strategy has been very successful and they have continued to invest heavily in quality control over the last five years.
In 2009, HTS TENTIQ introduced an SAP-based production system which controls the complete product and sales transaction from order input through production to delivery. All the product information is stored on the system and every part used has an individual part number that is linked to product groups during the production process. In 2016 HTS tentiQ completed fully linking its complete inventory system with SAP.
HTS TENTIQ currently has the following quality management certification:
- ISO 9001 Quality Management System
- ISO 14001 Environmental Management Certification
- EN 1090 Execution of steel structures and aluminium structures
- NB 2276 –CPR-001 / 15 – EN 1090 Conformity of Production Control
In 2013, HTS TENTIQ created a specialist Goods Inwards Quality Control department responsible for the quality of incoming components, and all HTS TENTIQ suppliers must have an active QS system and be ISO accredited. All incoming goods are subject to quality control checks. In November 2017 HTS TENTIQ finished building its latest 900m² warehouse extension which is specifically designated for goods inwards and storage. This has been built to help production workflow and increase efficiency and production capacity.
Green thinking
In 2016, HTS TENTIQ signed a recycling agreement with Texyloop to recycle waste product from its PVC cover production facility. In 2017 HTS tentiQ sent 8.5t of waste product to be recycled and this is expected to increase in 2018.
Strong and safe
All structures produced by HTS TENTIQ are subject to a Static Calculation which confirms their structures are suitable for the wind and snow loadings requested by the customer. HTS TENTIQ have their own in-house Static Engineer and have designed and delivered structures that can withstand the most extreme climate conditions, including extreme heat, cold, wind and snow loads.
For the static calculations to be completed, a full set of drawings must be produced. All technical drawings are produced in-house by the HTS TENTIQ Technical Department and in 2017 HTS TENTIQ introduced a 3D computer-aided design (CAD) drawing system to improve quality and is currently investing in the retraining of all drawing technicians to enable them to use the new system.
As standard HTS TENTIQ offers the customer PDF structure Drawings (CAD drawings available on special request and subject to confirmation) Operating and Maintenance Manuals, part lists with part numbers and suggested spare parts list.
All products are subject to a standard two-year warranty, which can be extended on special request.
Packing, deployment and maintenance
For military customers HTS TENTIQ can offer a packing service based on the specific regulations and documentation supplied by the customer (currently supplied to the German and Dutch Military).
All parts can be bar coded and supplied with a label to customer specification (currently supplied to the German Army).
HTS TENTIQ can also offer a maintenance frame agreement for used tents, which includes the unpacking and inspection of returned tents, the supply of a separate quotation for repair work and replacement parts and the cleaning of all parts, including the repainting on containers.
Should you have any additional questions regarding our organisation or products then please do not hesitate in contacting our office.