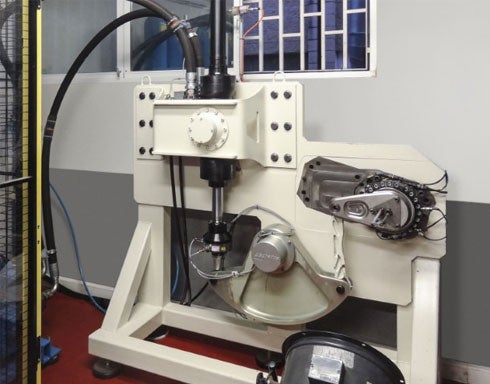
Moog Industrial Group delivered a test system for high dynamic rotary shock absorber testing to Piedrafita, a Spanish company that delivers solutions for vehicle engineering and land platforms. This robust fatigue test system will be used in the development process of a new shock absorber designed for military ground vehicles that work under extreme conditions.
When Piedrafita was working on the design of this new shock absorber product, the company needed a complex test system for the development phase and a robust fatigue testing system to ensure reliability. The company contacted Moog with the request to deliver a test system that could meet high performance specifications of 100g acceleration peaks, 4.4m/s velocity (14.4ft/s), 80kN (18kip) impacts and more than 300kW power transmission.
The solution that Moog delivered consists of a hydraulic servo actuator featuring 90kN (20.2kip) force at 280 bar (4,000psi). The high dynamic and low friction actuator contains a Moog D792 3-stage Servo Valve with 1000l/min (264gpm) flow and internal vibration damped electronics. The solution also comprises a control cabinet with a Moog portable test controller and software featuring special safety scripts.
Piedrafita commercial director Cesar Gonzalez commented on the performance and benefits of the system: "The Moog D792 Servo Valve characteristics and the test controller allow us to perform, in a single test bench, all shock absorber working patterns, including impact or step response tests, where peak speeds in excess of 4.5m/s (14.8ft/s) are reached. At the same time high frequency, small movements can be accurately reproduced.
"The short time between system definition and test bench commissioning was a key factor in the development of this product. The high dynamic characteristics of the system allowed our engineers to reduce the development time by concentrating different type of tests in a single session. The Moog team supported Piedrafita in a comprehensive way, helping in every aspect including test reporting, automization, bench safety, hydraulics and more."
In the past, dedicated test systems were needed for different types of land platform shock absorber tests, such as high frequency, low amplitude movement tests (wheel bouncing over the surface) and high displacement, low frequency tests (impact on obstacle at high speed). This made the testing of a mix of patterns complicated and time consuming. The Moog test system allows Piedrafita to perform both types of tests with one system, saving time and costs.
By using the system, Piedrafita has met the ambitious goals and planning of the qualification tests. The design verification and validation testing projects and also the accelerated lifetime test program have now been concluded. Currently a special working condition test plan is being executed. "We chose to partner with Moog because of the performance of the test system, but for Piedrafita the key factor was the commitment of the Moog team, helping us with the technical choice of components, supporting at 100% the right installation and commissioning under extremely tight time schedules," said Cesar Gonzalez.