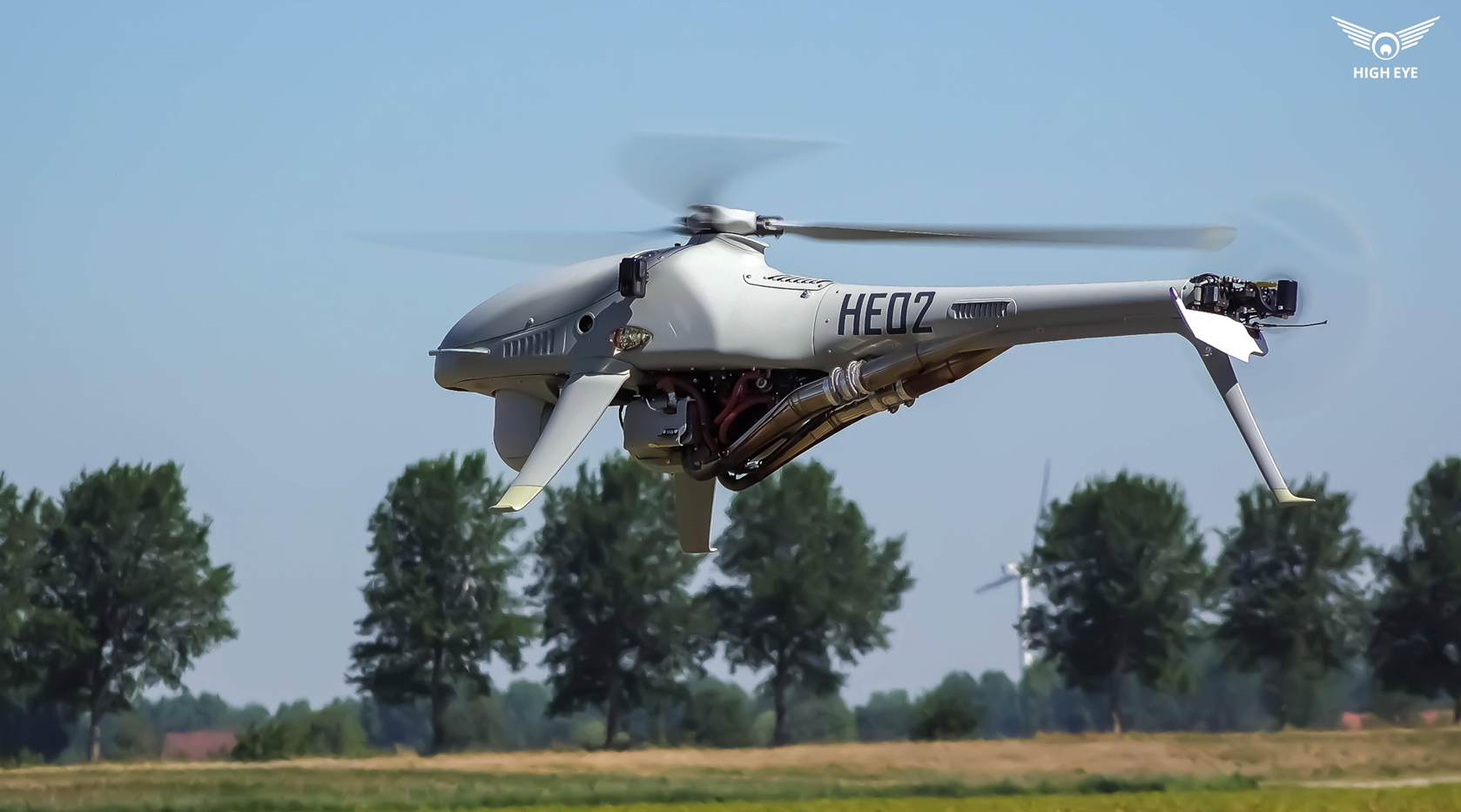
The right cooperation makes the difference
High Eye is a company that specializes in manufacturing the Airboxer VTOL UAV, a heavy-fuel driven (Jet A-1) unmanned helicopter system for both civilian and military use. In 2021, it introduced the Airboxer, a long-range drone with a single three-bladed rotor that quickly gained popularity in the market due to its small size, lightweight design, and ability to function in extreme conditions.
The Airboxer is a multifunctional ISR (Intelligence, Surveillance, and Reconnaissance) platform that is able to access locations that are difficult for other systems to reach. It has an endurance of 3 to 4 hours and can carry a payload of up to 7 kilograms, with a maximum take-off weight of 32 kilograms. The NATO STANAG 4738-compliant platform can be adapted to a variety of mission requirements or applications and can be easily integrated into challenging environments. Some potential uses for the Airboxer include coastal patrol and environmental control in the maritime domain, disaster management and border protection in the security and safety domain, and remote monitoring and power line inspection in the research and inspection domain.
To ensure the reliable transmission of media, the Airboxer utilizes plug-in connection systems from ODU, a leading international supplier of connectors. Ensuring the safe and efficient operation of the Airboxer is a top priority for High Eye and its customers.
Interview with Joost de Ruiter, CEO and owner of High Eye
- High Eye started with model helicopters in 1998 and over time has developed into a specialist for unmanned helicopters. What new technical challenges did you have to overcome and new regulations did you have to comply with?
Some of the key challenges we have encountered include:
Developing reliable and safe control systems for the Airboxer VTOL UAV. Ensuring that the aircraft can be safely and accurately controlled is a critical part of our work, and we have had to design and test a variety of control systems to achieve the desired level of performance.
Developing lightweight and durable aircraft structures. One of the key requirements for any unmanned aircraft is that it is as lightweight as possible, to maximize its payload capacity and extend its range. At the same time, the aircraft must be strong enough to withstand the stresses of flight. Finding the right balance between these competing demands while complying to NATO norms, such as STANAG 4738, has been a major technical challenge for us.
- And which new regulations did you have to comply with?
The regulatory landscape in the unmanned aircraft industry is complex and can be challenging to navigate. However, by staying up to date on the latest rules and guidelines, and by continuously adapting and innovating, High Eye could ensure that we are able to operate safely and effectively. We are working to obtain the Light UAS Operator Certificate (LUC), which is required for drone operations within the EU. This certificate allows us to assess the risks of our flights based on strict guidelines set by the European Aviation Safety Agency (EASA).
- The Airboxer was developed over a period of more than 8 years and tested under the most extreme conditions on several continents. What were your requirements for the Airboxer?
Mostly reliability and durability: Unmanned aircrafts are often used in a variety of challenging environments, and it is important that they are able to operate reliably and withstand the stresses of flight. The Airboxer is not an exception here – it had to be reliable and durable even when flying at the Arctic Circle in Canada, in the desert of Abu Dhabi or above the sea in South Korea.
- What technical challenges do you face from your customers?
Designing and integrating payloads (cameras, sensors, etc.) onto the Airboxer VTOL UAV. Our aircraft is often used for a variety of applications, and we had to design and integrate a range of payloads to meet the needs of our customers. This has required us to develop advanced techniques for integrating cameras, sensors, and other payloads onto the aircraft, while minimizing their impact on the aircraft’s weight and performance.
- You have been working with ODU for years. In which areas are the plug-in connection systems used?
We are using the ODU AMC® connector for our ground control system as those are highly respected connectors that are widely used on various Dismounted Soldier Systems. We appreciate its easy handling and robust break-away design, making it ideal for military and security power applications. This connector is designed to withstand rugged conditions and has been tested to meet MIL-STD-810H standards. The GCS (Ground Control Station) module is the central hub for all ground control equipment and is responsible for operating the flight control software and managing all telemetry communication. It communicates with the Airboxer, antenna systems, and pilot control unit using Ethernet.
- What requirements do you have for the connector systems and how could it be implemented?
Our company is dedicated to producing high-quality VTOL UAVs. The requirements for connectors are the same: they need to be able to withstand even the most extreme environments. Whether it’s scorching heat or frigid cold, our ground control station is designed to function with reliability. We understand the importance of dependability in these types of situations, and we go above and beyond to ensure that our products meet and exceed the end-user expectations.
- What distinguishes your cooperation?
The cooperation between High Eye and ODU is marked by several key features that set it apart. One of the main distinguishing factors is the focus on safety and reliability. Both companies are dedicated to manufacture products that are safe and efficient to use.
Another key aspect of the collaboration between High Eye and ODU is the ability to customize and tailor solutions to meet the specific needs of their customers. Whether it’s adapting connectors to fit specific requirements or developing bespoke payload capabilities, both companies are committed to provide solutions that are tailored to the unique needs of each client.
However, I also think that both of our companies are constantly looking for ways to push the boundaries of what is possible and to develop new technologies that will help our customers achieve their goals. This focus on innovation is what sets our collaboration apart and helps to ensure that we remain at the forefront of our respective industries.
ODU Group: global representation with perfect connections
The ODU Group is one of the world’s leading suppliers of connector systems, employing 2,500 people around the world. In addition to its company headquarters in Muehldorf a. Inn (Germany), ODU also has an international distribution network and production sites in Sibiu/Romania, Shanghai/China, and Tijuana/Mexico. ODU combines all relevant areas of expertise and key technologies including design and development, machine tooling and special machine construction, injection, stamping, turning, surface technology, assembly and cable assembly. The ODU Group sells its products globally through its sales offices in China, Denmark, France, Germany, Hong Kong, Italy, Japan, Korea, Romania, Sweden, UK and the US, as well as through numerous international sales partners. ODU connectors ensure a reliable transmission of power, signals, data and media for a variety of demanding applications including medical technology, military and security, automotive, industrial electronics, and test and measurement.