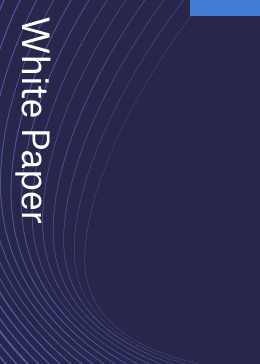
Reducing Risk and Accelerating Time to Market with Turret Aiming and Stabilisation
By Curtiss-Wright Defense Solutions
Tanks and infantry fighting vehicles are often moving across very rough terrain at high speeds while engaging an enemy.
For the safety of the personnel on board and the accuracy of the weapon systems on board, the turret aiming and stabilisation systems on these platforms must enable steady and precise control in all conditions.
Designing a robust, reliable, and high-performance turret drive system from the ground up is an extremely ambitious undertaking. It requires very specific engineering expertise in each of the key components; rotary gear drives, linear drives, gyroscopes, motor controllers, and hand controllers, and knowledge of how they interoperate.
Getting the design right and ensuring the system undergoes adequate field testing adds significant time, cost, and risks to programs.
The challenges associated with designing a turret aiming and stabilisation system are many and varied. For example, to operate reliably and accurately at any speed on almost any terrain, the system must deliver extremely high performance in a rugged and reliable form factor.
But the very stringent size, weight, power, and cost (SWaP-C) requirements on highly space-constrained weapon platforms often make that combination difficult to achieve.
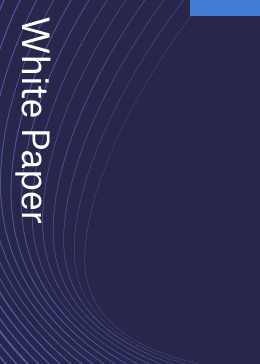