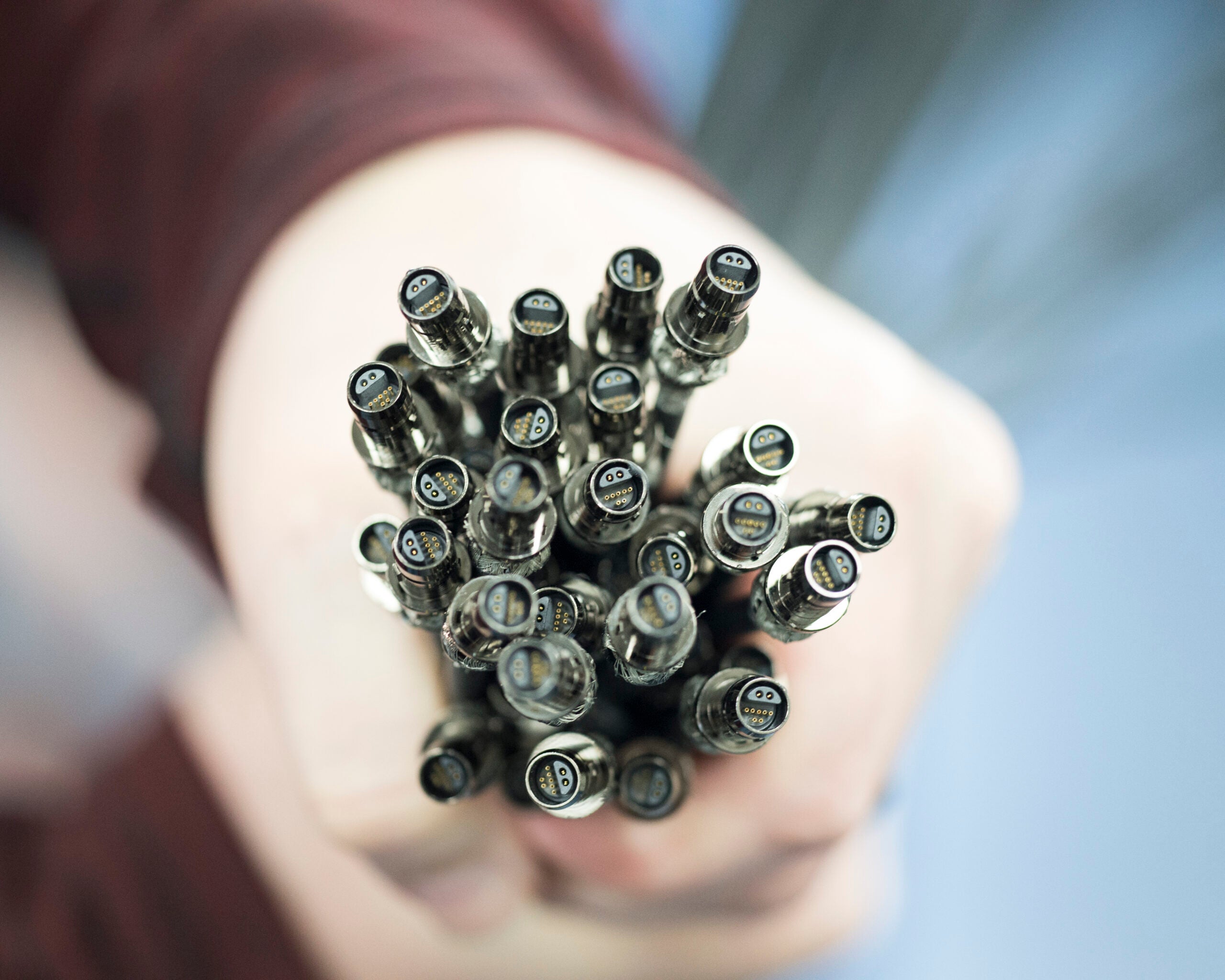
The demand for ever more portable electronic equipment is pushing the limits of conventional connector systems. From everyday electronics to medical, military and deep space environments, today’s applications demand equipment that is more compact and rugged than ever before, while delivering the highest quality signal processing. Designing smaller connectors is a careful balance between size and function. The question is: how small can they go?
Small is powerful
Connector miniaturisation is being driven by the ability of modern circuits to run on a lower voltage and current while running faster, storing and processing more data and protecting battery life. At the same time, chips are moving closer to the action, where they need to handle low signals at short distances. For example, they are increasingly found at the end of arm in robotics. Smaller connectors have also been shown to perform better in high shock environments, since they have less mass and are less affected by the laws of acceleration, making them ideal for certain rugged environments.
As medical, military and aerospace technology makes unprecedented advances, industries are demanding smaller and lighter connectors for portable electronics. The applications are as diverse as camera interface positions in surveillance equipment, unmanned aerial vehicles carried in backpacks, goggles worn by military personnel and medical endoscope cameras and prosthetics.
New manufacturing technology, such as design software and computerised numerical control equipment, is making it possible to design and manufacture smaller connectors faster and more cost-effectively. Many connector manufacturers now offer online design consultation and a few-days turnaround on new connector formats.
Miniaturised ambitions
Just how small a connector can be depends on its electrical and physical requirements. Cable design has become a significant factor, as well as insulator material, pin spacing, and shielding requirements.
Miniature connectors must still preserve signal integrity. Connectors must offer a low enough resistance interface to meet the electrical current load for the circuit. The current limit is usually determined by the wire diameter. Connectors and circuit modules operating in a smaller space must also still protect against signal cross-talk and interference, which can be achieved through advanced shielding technologies. For many applications, signal must be maintained even in rugged environmental conditions, which could mean high shock or vibration, extreme heat and cold, or immersion and salt spray. As miniaturisation progresses, new protective elements will be needed, such as smaller elastomeric seal rings to keep out moisture.
IEEE 1394 wiring techniques and the use of low-dielectric-strength insulator materials are enabling excellent transfer of higher speed digital information without interruption. Newly adapted hook-up configurations can eliminate cross-talk, and impedance control and drain wires prevent jitter and noise, allowing very small connectors to handle gigabit signal transfer rates. Keeping size small and reliability high increases in difficulty as connector pin count increases, but mixing both male and female pin and sockets in the same half of each mating connector can offer a solution.
Today, custom and hybrid pin and socket designs are on the rise. Hybrid or mixed signal connectors combine mid-current and low signal circuits, mixing large and small pins in the same connector. They enable signal, data and power to be transmitted in a single connector footprint, saving space without sacrificing power requirements. Omnetics’ Micro hybrid connector comes in Micro-D rectangular configurations and circular configurations.
We are yet to see how small electronics can go. Circuit design continues to improve, combining signal systems for fewer lead counts. Careful use of shape and spacing is allowing new levels of high-density interconnection, and routing limits on printed circuit boards are being overcome, with high-density arrays routing flat flex-like cables into and out of highly stacked sets of boards to further reduce the weight and size of electronics. The latest trend uses flat array grid or interposer connections. The aim is to achieve the minimum size that still meets performance criteria.
Miniaturisation in action
Miniature and ultra-miniature connectors are creating new possibilities for what electronics can do. Omnetics’ polarised nano connectors (PZNs) are ultra-miniature connectors specifically designed to offer constant signal integrity processing in high shock and vibration applications. They are designed with military standard proven spring pins and up to 30-gauge Teflon insulated wiring, with pins and sockets plated in nickel and gold to ensure constant contact. Their current applications include controlling robots, triggering cameras in airports and monitoring biomedical data. They are often used for robotic prosthetics, where miniature signals are continuously running back and forth. In unmanned aerial vehicles, miniature connectors can help reduce weight and extend flight time.
The key is to see how tiny we can go while ensuring signal integrity, and the limits are being constantly tested. Connectors are rapidly redesigned to match their diverse applications and stay ahead of ever-evolving high-speed circuitry.