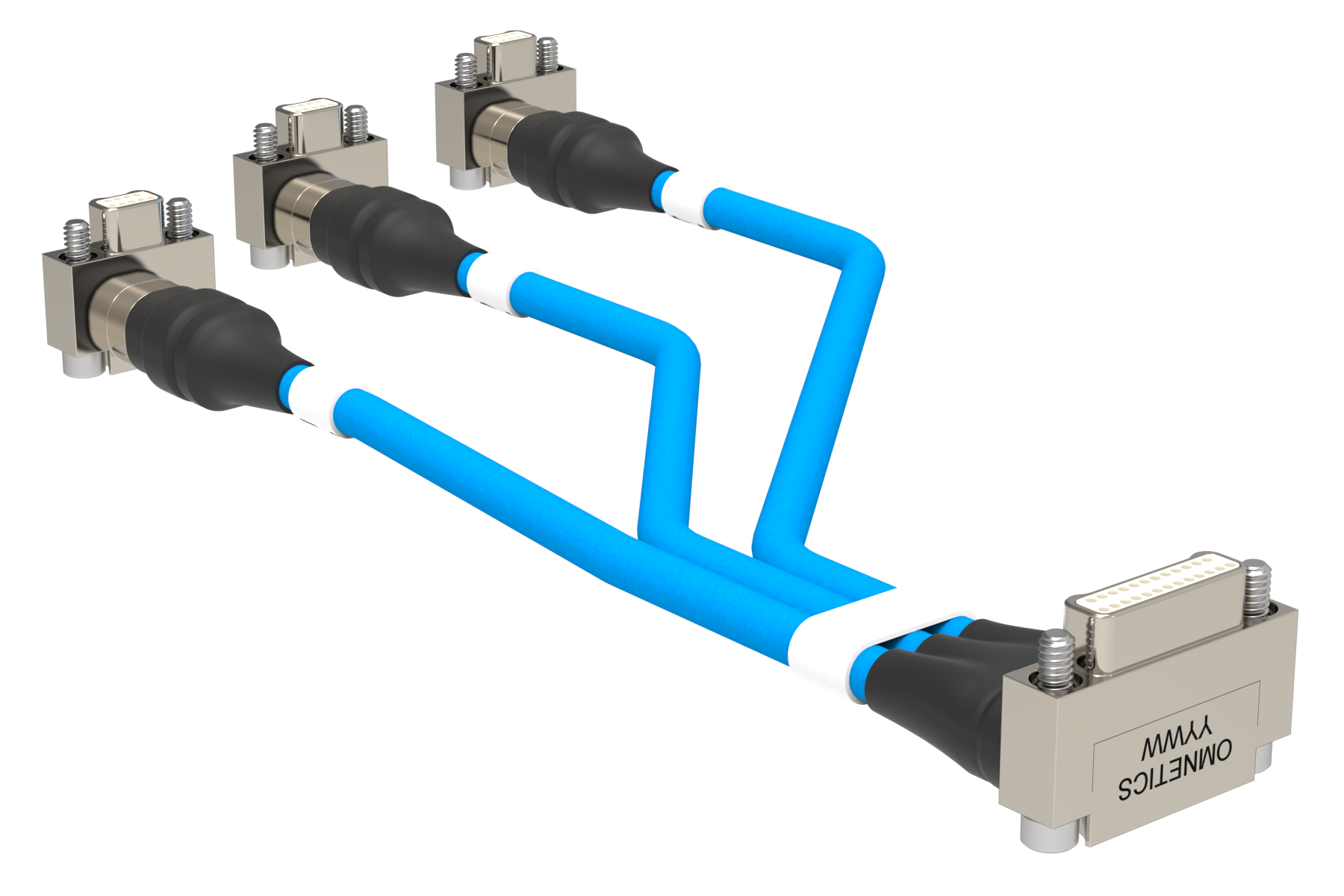
Whether you have exact designs and specifications for your complex harness or are looking for a partner that can provide expert advice and guidance, Omnetics’s experienced engineers can provide a solution. Quickly.
The first step Omnetics’s engineers take is to have an in-depth conversation with the customer regarding their complex harness needs, its applications in equipment and their intended use. Once that has been determined, the correct materials are assigned, together with all other accompanying information, which is then used to create a prototype drawing.
This drawing is reviewed between Omnetics’s engineers and the customer to verify all points have been addressed, as well as provide a visual of the end product. A prototype is created by Omnetics.
This prototyping process can be straightforward when standard materials and designs are used. An Omnetics connector design engineer communicates with the customer so that a solid model of exactly what the customer needs is created. Once the customer finds the solid model satisfactory, they will receive a 3D sample of their design (which is made using an automated material-added process), usually within 24 hours.
The customer then has a physical sample to fit it into their new application, to test its performance thoroughly prior to giving final approval. If not, the design will be further adjusted or materials changed, going through further design-build-test-design cycles.
If the customer has design and material requirements that are not standard, Omnetics can still supply any design solution, and custom engineer cables and connectors to any specification, for any application and for any environment required.
Custom-engineered solutions
Here are some very brief examples of how Omnetics engineers have offered different solutions to clients for a wide range of applications and environments after discussing, modelling and prototyping.
Soldier-worn mobile applications: Omnetics would need to know any significant factors the customer requires in the harness’s performance and longevity, and whether it needs to be high flex, low weight, colour and durability. A cable with a high strand count wire in a small gauge (30 AWG) with a flat black finish may be proposed. If the standard connector is black but too shiny for the customer, Omnetics can easily propose a different black plating that meets the conductivity and corrosion resistance needs of the design.
Aircraft wings: Omnetics will need to know the temperature ranges they might go through, what chemical resistance levels are needed and the type of durability and shielding they require.
In Omnetics’s experience, solutions for these harnesses lean more towards Teflon jackets with plated fibre or wire braids for electrical insulation and isolation, followed by an over braid, to protect it from abrasion when it’s mounted inside of the wing. Here, materials may be chosen more for chemical temperature resistance and weight rather than appearance or flexibility.
A Teflon jacketed cable or wire may be switched to a lighter ETFE (Ethylene tetrafluoroethylene) jacket to save weight. Amberstrand® may be used to reduce the weight of the EMI protection over silver-plated copper wire for the braid. External abrasion resistance can be taken care of with an additional nylon or Kevlar braid over the whole assembly to protect it in areas where rubbing occurs during take-offs, landings or turbulence.
Cube satellites: These harnesses have strict requirements as regards size, weight and shielding. Omnetics has manufactured a number of different configurations for cube satellite applications. In most cases, they have used nano or hybrid-style connectors with the cables.
Their housing finishes are different from those for ground-based applications; some can be gold plated, while stainless may also be used for radiation resistance. Flex circuits may have additional layers of shielding on the top and bottom of the traces.
Shock and vibration are important considerations to keep in mind, at least until the satellite is in space. Once there, the main consideration becomes temperature fluctuations, which are generally more extreme: very cold when in the Earth’s shadow or very hot when in line of sight of the sun. Omnetics applies different encapsulants for different environments.
Underground applications: For mines or oil and gas drilling, the most important factors to be considered are temperature and chemical resistance. Omnetics usually suggests a stainless connector housing and high-temperature epoxy, as this combination does well for extended temperatures in excess of 150C. Teflon jacketed wire might also be offered as it is known for its temperature and chemical resistance.
A focus on the Omnetics design stage
Customers may have designers or engineers on staff who are experienced with cables and connectors. They would understand their system needs and, in many cases, have a well-defined plan in terms of wiring diagrams, lengths, temperature or environmental concerns and shielding needs for EMI/EMC prevention to list a few considerations.
In those instances, the design engineers at Omnetics review the documentation and requirements provided by the customer, to ascertain the product requirements and begin a dialogue.
Omnetics’s engineering and manufacturing departments are extremely experienced owing to the range of solutions they have created over the years. Discussions take place many times during a design dialogue to decide on what materials are needed to create a solution that is finally going to be manufactured.
Customers may require a specific braid, for instance, to obtain shielding values necessary for EMI protection levels for their application. If Omnetics has an alternative product in stock to the one the customer specifies, but which will perform as well or better, and can be used immediately to save cost, time, weight or improve flexibility, it is offered to the client.
Other customers may not have in-house experience or design capability to provide documents for Omnetics’s review. They may only know what needs to connect to which device, how far apart the connections might be and the environment it will end up in.
They may state a number of cable flexures and temperature ranges; that may be all the information available at the starting point. In this case, dialogue then begins further up the chain, in terms of Omnetics engineers devising and presenting potential solutions to the customer based on the harness’s application.
The prototyping stage
The range and frequency of checks carried out on a prototype’s design specifications are also performed on manufactured end products. Prototypes are created using equipment and material that will be used in final production runs. Leadtime is a major factor, and an occasional substitution or exception may be requested from the customer during this process.
Omnetics verifies all incoming materials and supplier-provided documentation and associated certifications to ensure customers will receive the highest quality products. Their physical dimensions are also checked, using a number of methods ranging from the traditional pin gauge on a hole to XRF to determine plating thickness. Wires and cables can and are meticulously checked, together with impedance or skew testing.
Crimps on wires are tested using pull testing, based on Nasa levels. Where shielding is important, resistance measurements are performed between the braid and shell, or shell to shell in the case of jumpers and harnesses.
Prototypes are sent to the quality control department to have some, or all, of the following tests carried out:
- Electrical continuity (in all wiring)
- Dielectric Withstand Voltage (DWV)
- Insulation resistance (IR)
- Physical checks for correct overall dimensions and visual/mechanical inspection
Going beyond jumpers and wires
One of the most satisfying things for Omnetics’s engineers is that because of their vast theoretical and practical experience designing connectors and cables, they begin formulating solutions almost before they get sight of any customer requirements.
A prospective automotive customer will have vastly different needs than say, a satellite manufacturer. So, they will go into any initial discussions with their mental ‘toolboxes’ ready, filled with materials relevant to the customers’ industry.
Their integrated connector solutions may contain hybrid material types for harnesses. They might specify a connector made by Harwin on one module within a system, while another uses one made by Glenair, all married with connecter and cables from Omnetics. The engineers will readily procure any third party connectors from the market to ensure the customer receives a product that will be the closest match to their design specification.
This phenomenon is particularly visible when lead time and/or availability are in question. Whenever Omnetics is faced with any of these issues, they are perfectly comfortable integrating and adding third party products to the mix.
It might also be the case that they find a mix of signals included in harnesses, where there is not only power, but digital signals from devices that may require the use of flat cables, special shielding or form factors found in the commercial and military applications.
For more information, please visit: https://www.omnetics.com/