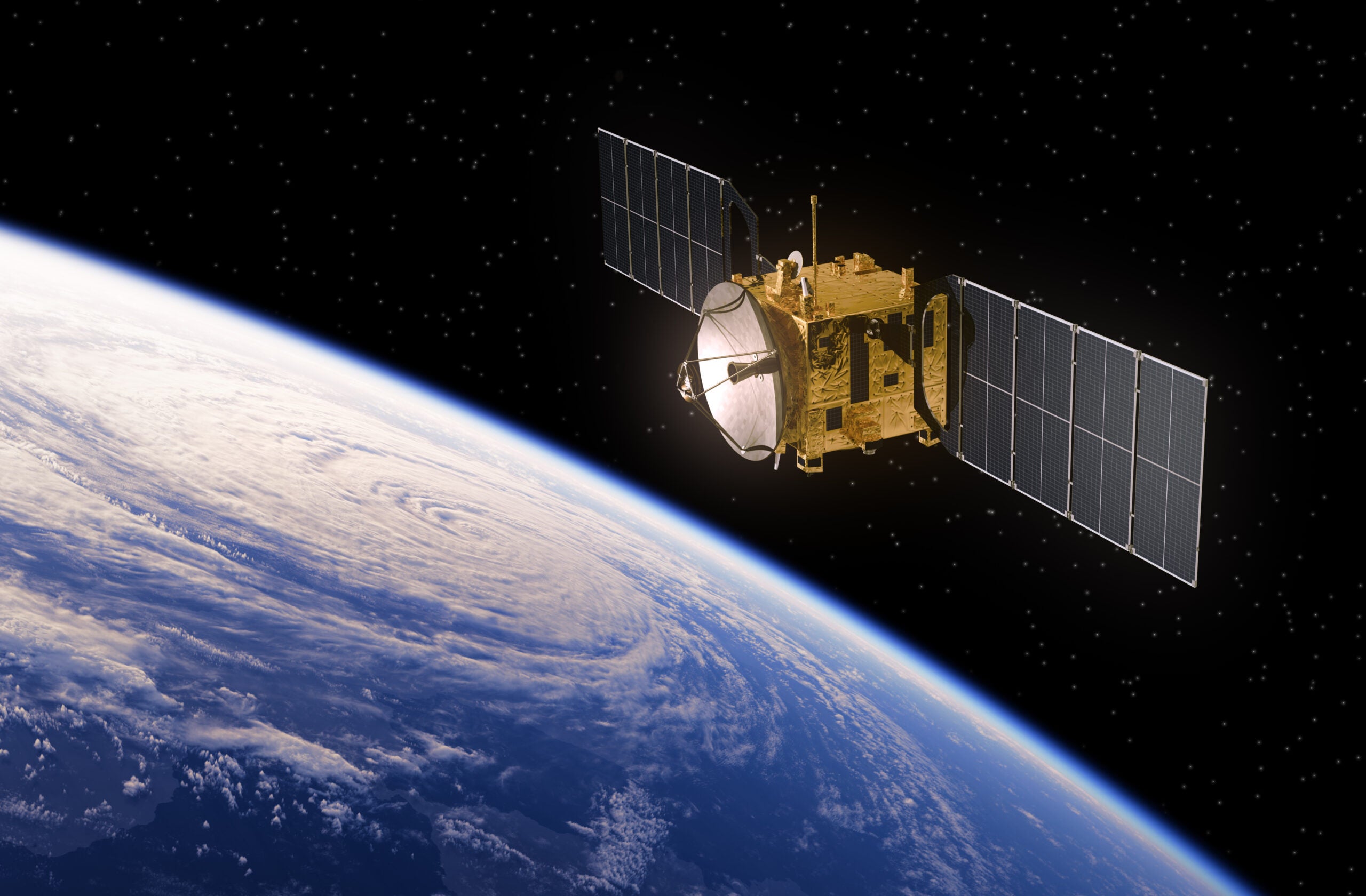
Omnetics has spent decades as a lead partner for national and corporate space programmes and continues to be the first choice of specialized rugged connectors.
August 5th this year marks the 10th anniversary of Omnetics connectors landing on Mars for the second time, installed as they were in Mars Curiosity’s mission-critical Miniature Inertial Measurement Units (MIMU). If not for their rugged performance parameters, the craft may not have landed safely on the red planet.
Big claims for a humble piece of equipment, but it demonstrates that each and every component in the SUV-sized Mars Rover had been designed and tested to perform beyond its call of duty. Some of the considerations Omnetics had to design ruggedized connectors for include thermal expansion within allowable ranges and ensuring low outgassing within them.
The dense connector and cable assemblies had to be of ultra-low weight. They had to be resistant to electromagnetic interference (EMI), crosstalk and high-speed problems using back-shells, strain-reliefs, braided shielding, and cables to extend the life of critical systems.
A fundamental Newtonian principle governs designs of electronic equipment bound for space – F=ma, or force is equal to mass times acceleration. So, one of Omnetics’ considerations when choosing materials from which a space cable/connector assembly would be built is their weight.
The lighter the assembly is, the better it will maintain the connectivity required, even under the highest G-force, vibrations, and shock it may experience on the launch and landing of the craft.
Quite apart from the high-profile deep space missions that glue us to our TVs periodically, there is a huge expansion in more prosaic, yet extremely important orbital space applications launching from pads around the world.
Every major nation, and many major global corporations, are undertaking lone or joint projects around space-bound aircraft that will take off and land from spaceports – Houston already has one – and satellites bound for low-, mid- and high-Earth orbits.
And all electronics hardware within them will need connectors.
Leading from the front
Omnetics has been at the forefront of connector designs for space technology electronics for decades and is a part of an elite group of global companies that ‘do space’. Until quite recently, its client list has been a who’s who in the fields of national military organisations.
However, there is a growing list of private companies that are reaching for the stars. And Space X, Virgin Orbit and Sierra Nevada, to name just a few, are already working with Omnetics. And many companies are sending up a ‘Smallsat’ or ‘Cubesat’, loaded with bespoke applications for their customers, on a shared-payload basis on satellite delivery vehicles.
Omnetics has positioned itself nicely for the future of near- and deep-space vehicle applications by carrying out joint R&D programmes with Amazon, Tyvak, ViaSat, NASA, Blue Canyon, Space X, Virgin Orbit, Blue Origin.
More frequent launches from more distributed launch platforms around the world are expanding the reach, and reducing the cost, of sending satellites into space. Many organisations have entered, or are planning to enter, this high technology sector, and the market for ‘Space’ is set to grow exponentially.
And so is the investment in it.
Space investments
Spire and Black Sky Global have garnered funds to invest in space applications, having convinced fund managers such as Bessemer Venture Partners, Lemnos Labs, RRE Ventures, and Vulcan Capital-investments, that this market, and their products and applications, are robust and will grow.
Spire offers a range of data services such as weather forecasts, location data for asset protection and plans to offer further new services. Black Sky’s persistent global monitoring services use an analytics platform, Spectra AI, that provides geospatial analytics and image collection, and can integrate third-party data to monitor global events and activities for enhanced situational awareness to help their clients understand and predict change.
Space-grade connectors are a natural progression from their military ancestry. Omnetics’ decades of experience in this industry means that they already have a huge inventory of tried, tested and proven designs for connectors. Its design engineers ‘produce’ 3D ‘solid’ models using software of any client-supplied cable/connector assembly design specification and application. It then finds the nearest existing ‘stock’ design and evaluates whether it can be adjusted to match requirements economically. If not, they can build to requirements from scratch.
Some conditions that Omnetics’ space connectors in planes and satellites are repeated shocks, vibration, and long flight durations. Protecting the electronics within vehicles from polymer outgassing is ensured by the careful selection of speciality materials used in their construction. It also offers ‘Power-Plus-Signal’ connector assemblies to further reduce size and weight.
Of course, Omnetics MIL-DTL-32139 Nano-miniature connectors are approved for space programmes per EEE-INST-002.
Space connector considerations
The latest high-speed chip technology circuit boards installed in space vehicles are stacked to save volume. They interconnect using small, ultra-low-profile round or flat cables to gather and transmit data from one section to another in the device. Occasionally, these connector/cable assemblies are used to route both power and signal, so Omnetics will employ a specialist ‘interconnect’ design engineer to ensure its fabrication meets client and application specifications.
Omnetics’ engineers analyse the client design and specifications for size, space, weight, and application considerations (environment, shock/vibration, thermal cycles, radiation, EMI, cyber security, length of use, outgassing).
Further considerations related to a ‘rugged’ design that will take into account the thermal profile of the application and installation environment (orbital condition) the unit will face continually for extended periods of operation. Nano-interconnect systems can also be designed with further consideration given to backshells, strain-relief mechanisms, braided shielding material and high-temperature epoxy to improve handling and extend its life in client systems.
Further details:
For more information, please visit Omnetics Space Connectors