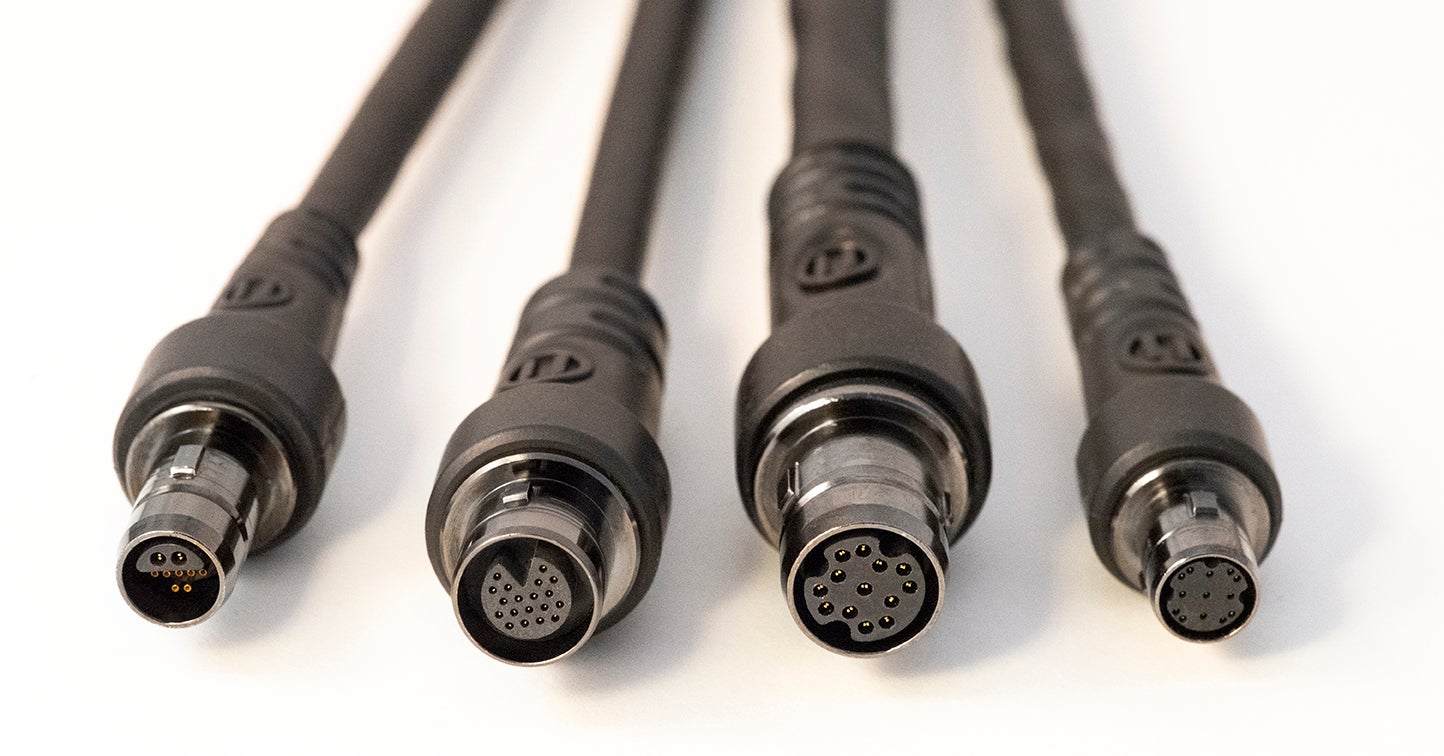
Connectors. This most prosaic-sounding piece of kit is so critical in maintaining power and data flow in the largest and the smallest piece of electronic equipment it is almost impossible to overstate their importance.
For example, mobile phones might have any one of these sockets for data and power transfer: Micro-USB, Mini-USB, Mini-USB-A, Mini-USB-B, Mini-USB-C, Apple’s Lightning, and a further dizzying variety from mobile manufacturers with non-standard versions.
Your television and computer will have a selection of these: USB, USB-C, HDMI V 1.2, V 1.3, V1.4 and V2, Firewire, RJ45, Mini DisplayPort, DVI–I, DVI–D and DVI–D Dual Link, Mini DVI Connector, VGA; and this is not an exhaustive list.
The above is just to give you an idea of the bewildering range of connectors that are in use at the moment in just a couple of types of electronic devices. Across all electronic devices, the number is huge.
The miniaturization of devices is leading to new thinking in how best to achieve connectivity and maintain it through any force that may be applied to it. This is where the importance of ruggedly designed and light smart connectors that remain reliable and continue to function through shocks, vibrations, or impacts.
Military applications
Yesterday’s connectors are less of an option to meet the demands in the highly aggressive mission-critical battlefields of today. Often, Mil-DTL-24308 and 38999’s are simply too big and heavy, as they were designed for older, larger bulkhead-type panel mounted systems used more traditionally on aerospace applications as opposed to soldier-worn.
An important market for such miniaturized connectors is in-man-portable electronics devices for military use. Soldiers nowadays are carrying more computing power than ever, and each device they carry will go through many different use cases. They used to carry just radios for communications, but now they may additionally be carrying cell phones, GPS devices, computers, night-vision goggles, as well as being a Wi-Fi hotspot for their colleagues to send and receive real-time battle data.
These, and all other portable devices, have one thing in common – all need rugged cables and connectors capable of transmitting data and power in some of the harshest environments anywhere. Cables and connectors for soldier-worn devices are demanding reduced sizes and weights, and also that they should be much more flexible as even uniform garments are becoming digitally enabled.
In general, military applications are pushing connectors to be more SWaP friendly, (Size, Weight, and Power). In other words, towards being smaller, lighter, and capable of carrying more data and power for applications such as space vehicles, smart munitions, missiles, communications, and a host of others, including combat uniforms.
Body-worn applications
Jackets carry power and data from source to destination through cables and connectors woven into the material, using round or rectangular small ruggedized Nano D-Sub miniature connectors that are manufactured to MIL-DTL-32139 to ensure they continue working in mission-critical applications.
Set to .025-inch contact spacing, these shells are precision machined and can withstand the high shock/vibrations of harsh use in military vehicles, dangerous levels of temperature, and the most hostile environments possible – down a hole in the ground, where temperatures can rise to between 35°C to 40°C, down to -270°C in the frozen expanses of space.
New designs in military helmets often mount displays to help the wearer see better in low-light situations. With a suitable face screen, they can also receive information from battlefield commanders.
The Italian Soldata Futoro, (Future Soldier Program), raised soldier-worn technology to the next level. Starting with the uniform itself, the material was designed specifically for temperate and desert environments in which many of today’s battles are being fought. Woven within the material are small, ruggedized Nano Subminiature D connectors that match MIL-DTL-32139.
These connectors pass data and power simultaneously underneath the body armor and are protected from stab and blast damage. Helmets were also redesigned to feature two visors, (splinter and bullet-proof), as well as helmet-mounted displays (HMD) that present information from a low-level TV camera mounted on the back of the helmet. This unit is also night vision capable.
Power and signal supplies
Powering and supplying signals simultaneously in one miniaturized cable has been key to increased mobility and safety of the battlefield troops involved. Cable with both power and high-speed digital signal processing requires new and additional wire system design and jacketing. To assure strength and environmental resistance while maintaining flexibility and small diameter cable materials have also changed.
All connector/cable combinations must be able to deliver power and clean data streams, undisturbed by electromagnetic interference or pulses, and continue working perfectly through USB 3.0 (5 Gigabits per second) and HDMI 2.1 (up to 48 Gigabits per second) connection speeds while being much smaller than 1cm in size. But even though they are small, they must be able to be easily connected/disconnected under battlefield conditions.
This simple-sounding activity is, unfortunately, not quite so easy to perform in real life. Small jackscrews, while well-proven in shock/vibration situations, are fiddly to mate in the field. Micro-D and nano-D connectors have hex screws, but without a suitable driver, getting them mated is a pain. So what was needed was a connector type that was easy to mate, yet robust enough for all conditions.
Enter the design geniuses at Omnetics. Their new latching micro-D’s and nano-D’s are now readily available and have proven to withstand any and all of the rugged shock and vibration tests. These changes allow for faster change over and eliminate the use of carrying hand tools on the battlefield which can be mated by gloved or bare hands.
Signal shielding and isolation
Additionally, EMI shielding and ensuring cyber isolation requires improved shielding methods, often using multiple shields and drain wire methods. Conventional HDMI cables use shielded twisted pairs for everyday household use but for the battlefields, these cables must be smaller in diameter and must include multiple strand elements, as well as the inclusion of separate, shielded wrapped pairs with assigned drains per pair.
New specifications too are being written to accommodate these designs in an effort to help achieve very high-speed digital signal quality for the applications. Nano-miniature connectors are no different and require being wired differently. Protecting the impedance coupling from set to set implies new wiring layouts within the connectors.
Power sections are also isolated as part of the connector design and match up with the cable. Finally, the process of over-molding the connector using a polyurethane material bonding to the same polyurethane cable jacket assures IP-68 moisture protection and strain relief on the cable to connector interface.
Meanwhile, deep inside the connector, the pins and sockets are designed to full military specifications and are gold plated to assure more than 2,000 mates and de-mates. This provides long-term reliability of the new power and signal cable throughout the battlefield duration.
Portability is key
Additional demands for military portability of powered circuits and connected/signal interconnects are emerging regularly in the form of soldier-worn power distributions hubs, that securely and safely control both power and data distribution of a tablet computer, heads-up displays, etc, as well as a number of IP68 cable system designed to connect to a number of peripheral cables and the main power unit. As mentioned before, this system offers 5Gbps super speed USB 3.0 in rugged miniature form factors.
As we power up our modern battlefield electronic technologies, we see the evolution of miniaturized modules from sensors, cameras, communicators, and actuators. Circuit chips now run on lower voltage and current levels while the data is routed shorter distances. This trend embraces the use of smaller, lighter electronics all around.
This trend also allows highly portable power systems to be integrated into one common cable routing system and lower current carrying connectors. We are also seeing new cutting-edge connector securing options that reduce the use/need for tools to mate and de-mate connectors.
Thanks to miniaturization, mobilized ground troops today can carry much of the latest high-tech equipment and technologies, process and distribute data among their mission team more easily and without fear of power loss or of interruption.