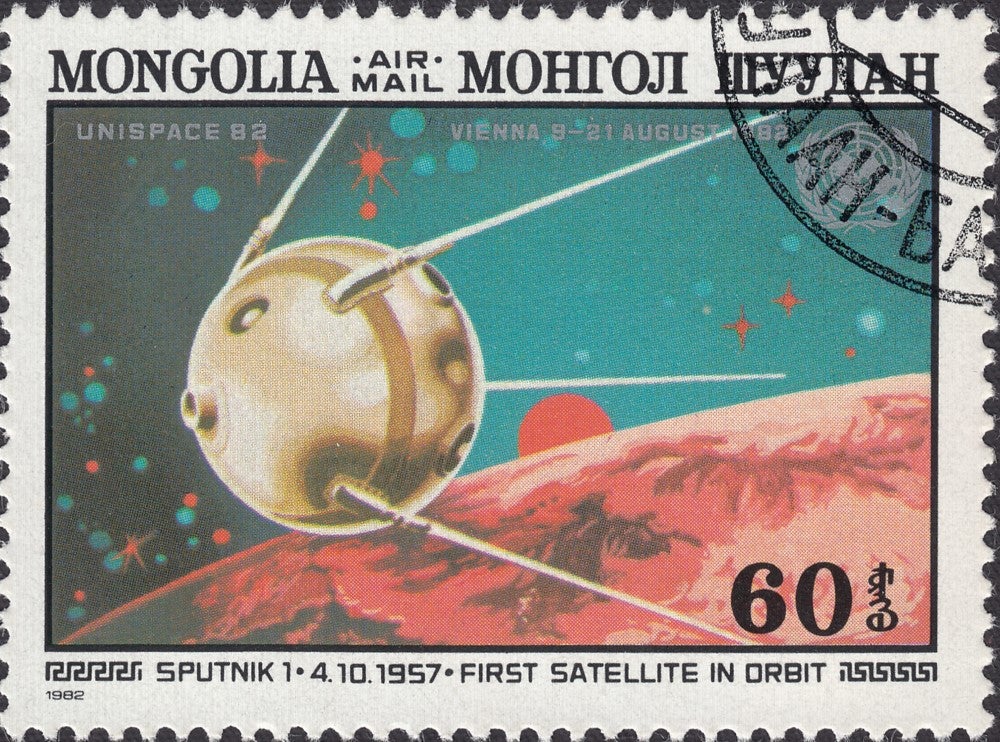
They started small, when on October 4, 1957, the Soviet Union successfully launched Sputnik I, the world’s first artificial satellite. It was about the size of a beach ball and had four antennae sticking out from it. It weighed just 83.6 kg (183.9 lbs) and took about 98 minutes to orbit Earth on its elliptical path.
Sputnik I made it possible to test satellite pressurisation, to study both radio wave transmission and the density of the atmosphere and allowed scientists to learn how to track objects in orbit.
Advent of nanosatellites
The latest trends, however, are for smaller satellites, called ‘CubeSats’, which come under the umbrella term ‘nanosatellites’. These are usually vehicles carrying a specific set of applications for their owners – communications, global positioning systems (GPS), weather mapping, imaging, oceanic monitoring, or any of a diverse set of functions – and they are becoming smaller.
They are defined as any satellite weighing between 1 to 10 kg that must comply with specific criteria that control factors such as their shape, size, and weight.
They range in size but are all based on the CubeSat unit, which is a cube shape measuring 10x10x10 cm and a mass of between 1 and 1.33 kg called 1U. This modular unit was expanded after the first few years, and larger nanosatellites are now widespread (1.5U, 2U, 3U, or 6U).
These are usually placed in Low Earth Orbit (LEO), which is Earth-centred at an altitude of 2,000 km (1,200 mi) or less; most are placed at between 750 km to 1000 km. According to a report by Erik Kulu, creator and analyst at the European Union’s Nanosats Database, there have been just under 6,000 such craft launched up to August 2022, with another 1,700 predicted to begin orbit by 2027. According to Travis Neumann, special project manager at Omnetics Connector Corporation, the future looks bright for the satellite sector:
“Many companies that are regularly in the news are talking about setting up [satellite] constellations so the world can have high-speed internet, GPS, imaging data, and many other applications. Looking at the sheer numbers they are committing to, I only see it exploding.
“If we look where companies like SpaceX and OneWeb want to go, their numbers are going to increase dramatically. Additionally, there are many what we call new space-type companies getting into small and CubeSat-type solutions focused on making space more accessible to the world.”
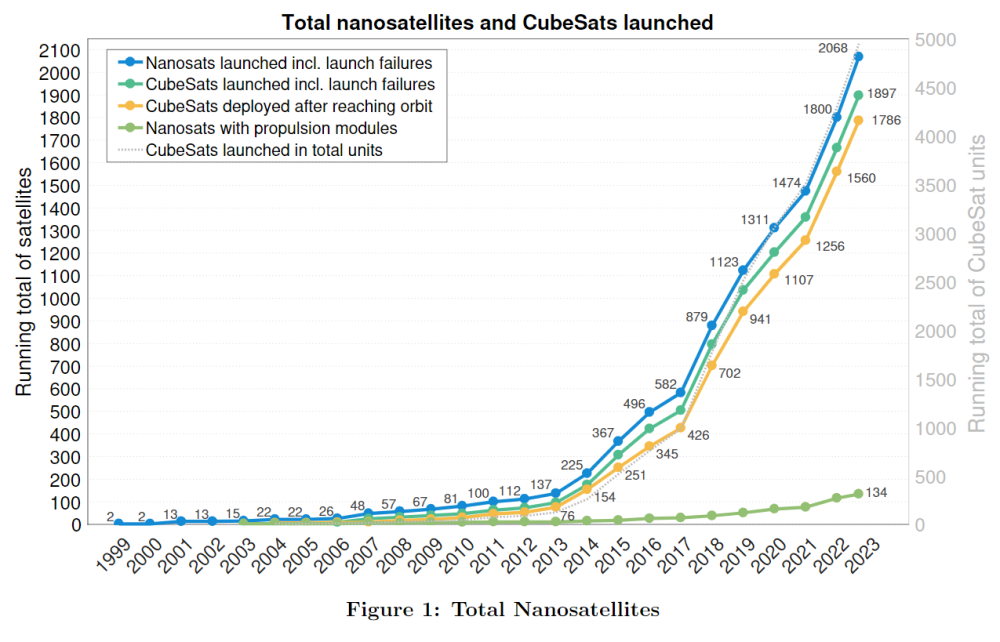
Electronics issues faced by satellites
The vibration caused by the launch vehicle is the first challenge that space electronics must overcome. There are high demands made on a rocket and its cargo during launch. Large shocks known as Pyrotechnic, or Pyroshocks, occur in the satellite’s body structure when it separates from the rocket in space.
Exposure to Pyroshocks can harm circuit boards, and short electrical components, and may result in connectors and/or harnesses becoming displaced from circuit boards of electronic devices.
According to Neumann, a recent order in Omnetics’s special projects division was building multiple harnesses for a California-based space/defence company, which produces software-defined radios, cyber security, and avionic solutions, but faced numerous hurdles
“We faced a few challenges with the three different orders they placed consisting of more than 20 different harnesses.”
“On the larger side are harnesses that require bundle management. We see them have specific heights and/or clearance they need to work around which means we must develop special fixtures and processes to ensure they can ‘fit’ and route properly within the craft,” said Neumann.
Understanding the launch environment helps to better appreciate the shock, and vibration demands placed on electrical components intended for use in space applications.
Issues caused by outgassing
Adhesives, glues, and plastics can and do release gases. Plastic device vapour has the potential to deposit material on optical devices, lowering their performance.
This issue in electronics is resolved by using ceramic components instead of plastic ones. The spacecraft can be surrounded by a cloud of pollutants due to the outgassing of volatile silicones in LEO. The external surfaces of the spaceship can deteriorate and change due to contamination from outgassing, venting, leaks, and thruster firing.
“One of the unique differentiators we have, is that in the past year, we brought in specialised IPC-620 space addendum training for our manufacturing technicians that are responsible for high-end assembly work for space applications,” says Neumann. “I’d estimate that more than 10% of our manufacturing staff have completed their certification, and there are regular classes here at Omnetics to support training for that level of quality.”
Omnetics has a long history of providing support for both orbital and deep space vehicles. Its products have been used in NASA’s Mars Rover (still operational) and the Space Shuttle program, which in turn delivered the CoStar (Corrective Optics Space Telescope Axial Replacement), a device to fix an error on the Hubble space telescope. The company also continues to partner with Iridium on solutions for their satellite constellations, which are orbital platforms for delivering communication solutions.