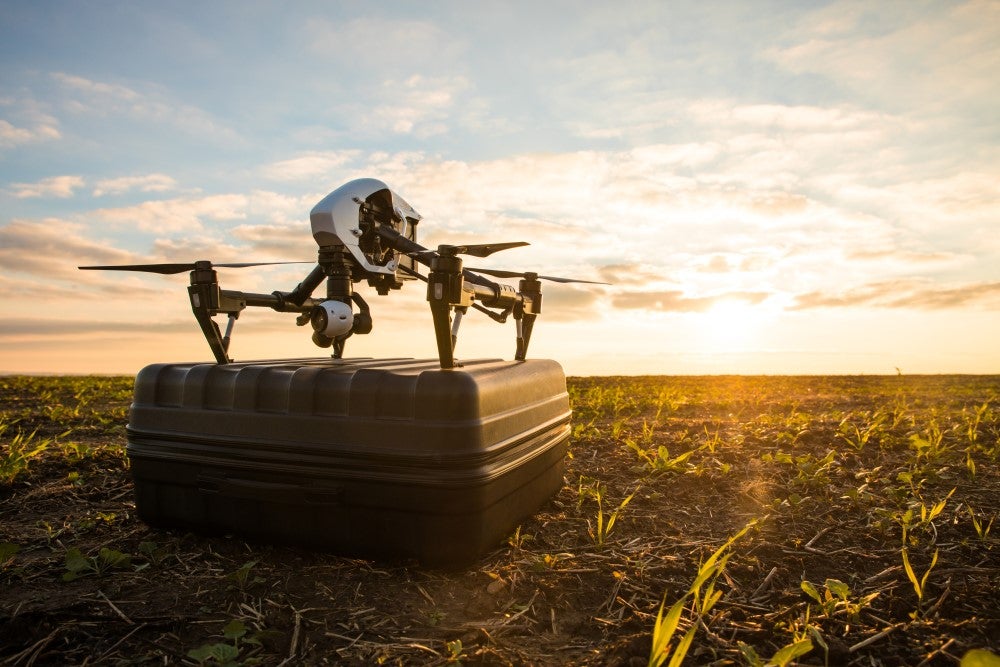
Unmanned aerial vehicles (UAVs) have continued to evolve since their inception in the early 1980s. With the beginning of the Predator drone push into the 21st century for military operations, UAVs have predominantly been associated with military applications.
Advanced sensors, tracking devices, attitude management systems, and other onboard elements have extended the reach, capability, and appetite for more integrated devices.
In more recent years, the attraction of drones has flown into the civilian sector with start-up companies focusing on police surveillance, agriculture, and structural integrity inspections of civil engineering.
Some applications have started to see these UAVs being used for delivery services, aerial photography, and 3D landscape modeling. As UAVs have evolved and grown in popularity, so has the demand to miniaturize their footprint, and integrate more electronics into their smaller frames.
Miniaturizing drone technology
With the push towards miniaturization, UAV manufacturers have understood the need for their onboard electronics to require smaller interconnect solutions, as more applications are being crammed into ever-smaller devices. The sizes of drones depend on their ultimate intended purpose, which also determines their size, power requirements, and sensor capabilities.
One example is that as drones decreased in size, they gave architects and civil engineers focused on infrastructure and building integrity the ability to inspect internal and external pipelines for cracks, building frameworks, and integrity by sending back images using low latency signal data and with high-resolution video (up to 4K). This has helped lower worker casualties across industry by enabling appropriately sized drones to access hard-to-reach locations.
Small hobbyist drones are generally available to consumers for personal and social uses, but the main drive towards miniaturization is in industrial drones that need to have high reliability to carry out critical tasks in sometimes hostile environments. It follows that suppliers of interconnects, electronics, and other materials for drone manufacturers need to be able to meet the demands for rugged and long-life equipment.
Specialised interconnect solutions
Having specialized applications means that having interconnect solutions to fit the wide variety of different types of drones is a necessity. A common situation regarding custom drones is that they need to have a hybrid connector that allows power and signal wires in the same housing. This combines two separate connectors into one, thus reducing the space it takes up, freeing up real estate for additional hardware.
As the connectors for UAV electronics get smaller, they need to be able to handle the shock, vibration, and harsh environments in which drones operate. Interconnect companies such as Omnetics have needed to adapt to the growing customer concerns and tackle the challenge of creating smaller connectors that are able to handle the rigorous qualifications on a smaller scale.
The miniature 38999 circular connectors have been largely adapted to the specifications of the older version of MIL-DTL-38999, due to its size and ability to withstand 3A on 24-30AWG wire. Omnetics’ UAV customers understand that these smaller interconnect solutions are available for their drone products and can provide the same high qualities of signal integrity and data transmission, regardless of the reductions in size and weight.
Changing payloads
UAV companies, focused on payload delivery to remote locations, have seen an increase in flight times due to the decrease in the size of the electrical components in the drone.
Drones have also begun to see a rise in the number and variety of sensors and electronics attached to their frames and gimbals to help fit the application, whether Light Detection and Ranging (Lidar), Forward-Looking InfraRed (FLIR) thermal sensors, First-Person View (FPV) Cameras, lasers, or radars.
It is virtually impossible for drones to produce high-quality video without a gimbal to absorb vibrations and shock. Gimbals mounted on UAVs are basically a gyroscope with motors to keep camera systems and sensors stable in flight, whether piloted or autonomous, regardless of extreme weather conditions.
As modern technology ramps up, the necessity for more sensors on drones as well as an increase in data transfer rates is becoming necessary. And the reduction in the size of interconnects has not altered the ability to push large amounts of data through smaller gauge wires and fiber optics.
When dealing with Lidar and 3D mapping, the millions of data points that are registered may need to be processed onboard prior to being transferred to the command area. Having low-latency data transfer is essential to a productive communication channel between drone pilots and UAVs for aggregating these large data files.
In addition to the issues with size and weight stated above, there are a plethora of other factors at work. There is a rising need for high-speed connectors because many of these lightweight military UAVs are equipped with cameras, weapons, GPS modules, and other detectors.
They are also called on to process large volumes of high-resolution video that must be transferred across connectors, which now have impedance requirements that weren’t a requirement previously.
These connectors also need to assist in preventing electromagnetic interference (EMI), so adding lightweight metalized braids may address important factors in signal strength to ensure the cable to the sensors is shielded properly, allowing improved signal integrity.
Omnetics connectors provide great density, unparalleled dependability, and high-speed data transfer in a variety of packaging, so UAV designers and manufacturers favor their solutions for all onboard flight hardware.