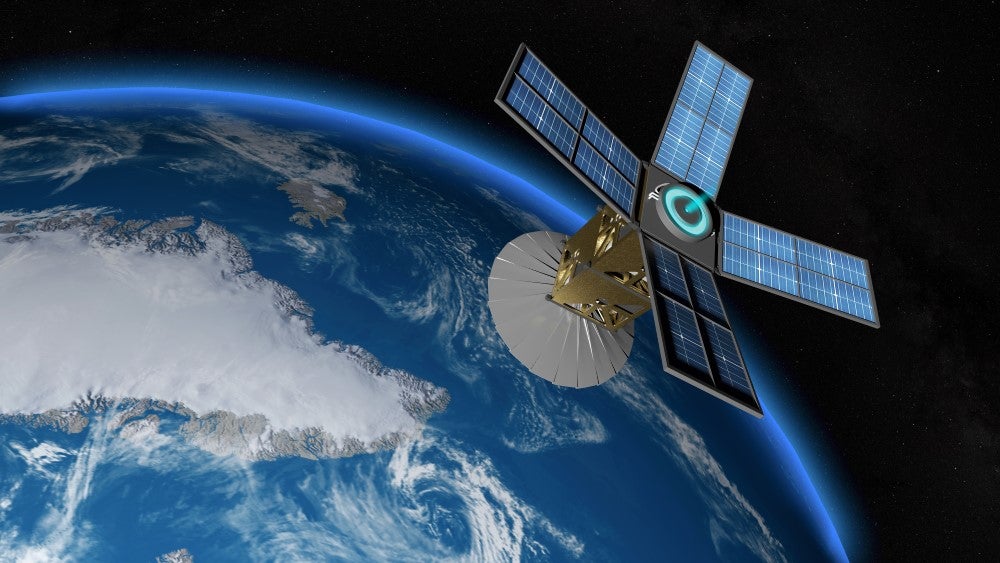
Decades of space vehicle investments are helping to support new satellite programmes which are both government-sponsored and privately funded, while commercial organisations and individuals are taking satellite technology and applications in a variety of directions.
These private endeavours are adding even more excitement to space exploration as some now have profit-based dimensions, while others are helping individuals achieve personal success goals.
Components for new satellite systems are frequently taken from devices that have already been tested and are made from the same materials and underwent the same processing.
This drastically reduces the period till launch and almost negates the chances of failures. In order to improve the quality and speed of digital signal processing, storage, and retrieval, a newer complementary metal–oxide–semiconductor (CMOS) technology has been developed.
The rules for current satellites have had to be rewritten by the move away from analogue processing. Newer chips have higher digital signal rates that can reach gigabit/second levels while requiring lower voltages and less current flow. There is also a reduction in the mass of the power supply, the processor boards, the cables, and the connectors.
Analogue to digital
Early satellites had big, heavy connectors. As they evolved, they began to reduce in size and, increasingly, micro-sized connectors and cables routing signals on 26-gauge wires in place of the more traditional D-sub connectors with pin spacing of 100mils were being used. More interconnections now use Nano-D connectors, which are 20% of the size and weight of earlier systems and use a pin-to-pin spacing of 25mils.
The reduction in mass and weight goes even further than that. The number and density of circuits made accessible to the satellite designer by choosing nano-connectors with 30-gauge wiring enable many more architectural functions to be accommodated within a single spacecraft. This dramatically raises the value and payback.
Satellites are rapidly adopting more electronic architecture, features, and services as a result of the digital revolution. Multifunctional modules with electronic flexibility that boost the contributions of each satellite deployed by combining features of older subsystems can be created.
To manage and route interconnected signals from higher-speed switching fabrics and quadruple the functional capacity of previously single-purpose elements, more onboard bus systems are being investigated.
Enter hybrid connectors
Mass and weight are greatly reduced by cramming numerous high-density processing boards that operate on their own backplanes. By working with VPX (a set of standards for connecting components in a computer) providers, satellite designers can greatly increase the effectiveness of their devices.
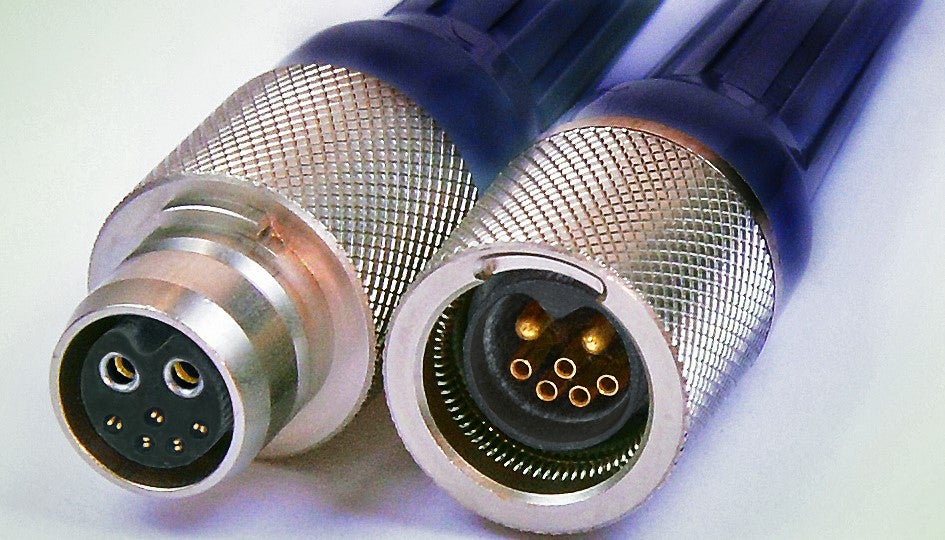
Utilising previously tested connector components, hybrid connector designs can quickly adapt to changing pin counts and power supply requirements.
Many businesses have circular and rectangular connection shells on hand or have them mechanically produced when needed.
New designs can be quickly transferred using reliable work models and delivered straight to the satellite designer for review. Changes are also being made to how RF (radio frequency) is used.
Rectangular or circular
According to Scott Unzen, Marketing & Market Development at Omnetics, “rectangular connectors generally comply with industry-standard design and tend to be used when one side of the connector is going to be mounted on a PC board or on a flex circuit due to simplifying the layout of the trace lines on the board(s).
“There are occasions that the rectangular design needs to be changed to a circular design such as when: the connector needs to be environmentally sealed, attached to a sensor or when a wire-harness/cable assembly needs to be feed through an assembled section; in these instances circular connectors are a better solution”, he added.
Coax connectors in the micro- and nano-size range are used in portable consumer electronics and by the military for ground troops. UAV surveillance systems require particularly lightweight transmitters in order to relay signals back to the ground. Designers frequently specify micro- and nano-sized coax connectors to stay within their weight and space constraints.
Geophysical mapping is one example of a function that can be executed concurrently while interacting with different Ethernet systems, each of which has its own format and set of codes. At gigahertz speeds, high-definition images can be recorded, saved, and retransmitted.
Old vs new
Electronics from both ‘Old Space’ and ‘New Space’ are constantly evolving to satisfy the needs of both commercial and governmental systems. Smaller and more dense circuits are enabling new applications in the satellite industry; older design techniques are blending with newer, quicker design techniques.
Although deep space research continues to present the greatest technological challenges, this development is being aided by more recent commercial orbital and sub-orbital spacecraft.
Electronic devices and components installed in space vehicles have been developed to perform in harsh physical and environmental conditions and to keep working because there is no option for them to fail as they cannot be repaired.
Electronic components that are relatively commonplace may be damaged by the strong shock and vibrations that a spacecraft experiences during ground launch. For instance, the connectors made by Omnetics that are mounted on printed circuit boards have to survive potential shearing caused by the high G-forces they undergo.
Mr Unzen told us, “The nano family of connectors will withstand the highest forces due to having the least mass. Additionally, the nano product family has variety of design options to meet the specific requirements of the design such as: rectangular, circular, strip style connectors, connectors with our without metal housings and hybrid options”.
F-ma
Newton’s second law (F=ma, or force equals mass times acceleration) is the governing principle behind the drive to make all space vehicle components as light as possible. Weight is the limiting cost factor for such craft, and designers strive to make devices small and dense so they can cram more functionality into a smaller area.
In order to maintain high signal integrity and ensure image quality, circuits that transmit digital photographs need to transport enormous amounts of data. To avoid distortion or “holes” in the image base, Omnetics systems are precisely matched to the impedance of the circuits.
In relation to applications Omnetics designed, Mr Unzen commented, “We have designed both circular and rectangular connectors for these types of applications the constant will be that each design will incorporate a metal shell to provide the necessary shielding.
“Some of the things that need to be taken into consideration in determining which form factor will provide the smallest form factor are what signal speeds/protocols will be transmitted, how many contacts are needed for the protocol and what is the optimal spacing between contacts.”
Evolving from the military to space
Some satellites at lower altitudes scan the planet for images and process massive image photos at extremely rapid frame rates, much like a high-speed movie camera. The electronic connector and cable design, as well as the tough dependability of the packaging, are crucial to the differential signal process.
Space-grade connections are frequently the offspring of connectors made for the military. The shells and mounting formats are modified by connection design engineers using solid model software in accordance with the new specifications according to the particular application it will be utilised. For the high shock, vibration, and lengthy flight durations the connectors are required for, quick modification to existing designs can be done affordably. Since the outgassing of some polymers can harm the electronics, specialised materials are required to safeguard the electronics inside the space vehicle.