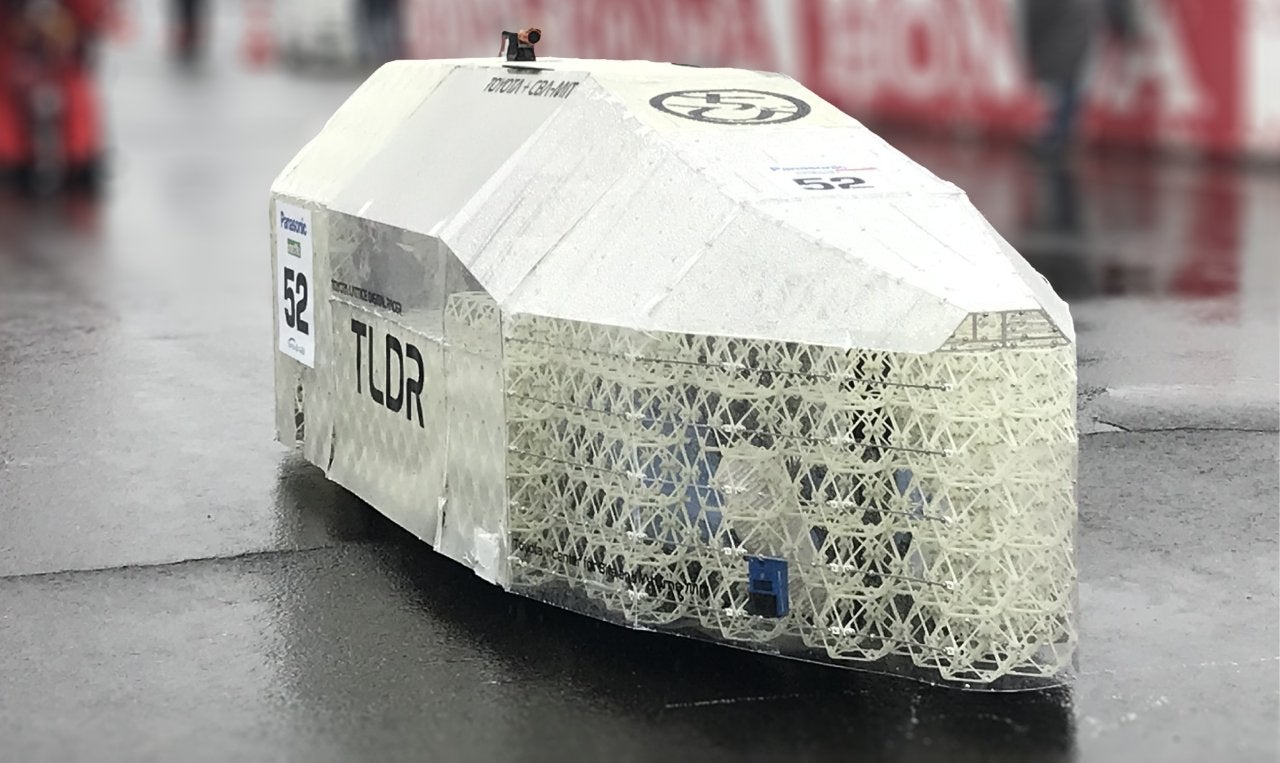
The US Army and the Massachusetts Institute of Technology (MIT) have developed a new way to connect metamaterials that will enable the creation of dynamic structures.
Developed by the scientists from the US Army and MIT’s Center for Bits and Atoms, the method link materials with unique mechanical properties using a discrete lattice system similar to Lego to develop structures with reconfigurable properties.
This technology opens up the possibility of creating military robots made of robots. For instance, a swarm of robots will be able to attach together to form a bridge allowing troops to cross a river.
If achieved, the capability will significantly enhance military manoeuvrability and survivability of troops and equipment.
The findings were published by researchers in the Sciences Advances cover story.
An army researcher Dr Christopher Cameron said: “Robots rearranging to form a bridge made of robots, similar to ants, is one embodiment of our concept of structural robotics, which blur the line between active and passive elements and feature reconfigurability.
“It is still a motivating use case for the system, but we are looking at broader implications for ground robotics which are adaptable, reconfigurable, and resilient.
“If a swarm of robots can turn themselves into a bridge, how else can they be rearranged? How do we design and control robots like this?”
The system leverages cost-effective injection moulding and discrete lattice connections to rapidly assemble macro-scale structures, which may include characteristics of rigid, compliant, auxetic and chiral material types.
The resulting materials can be utilised to develop cost-effective structures of larger scale compared to traditional metamaterial manufacturing.
In the subsequent phases, the research will focus on the design space created by the system with target applications such as modular soft robotics, impact-absorbing structures and rapid construction at the point of demand.
Researchers will also explore the feasibility of integrating conventional additively manufactured metamaterials with this system to combine their strengths.