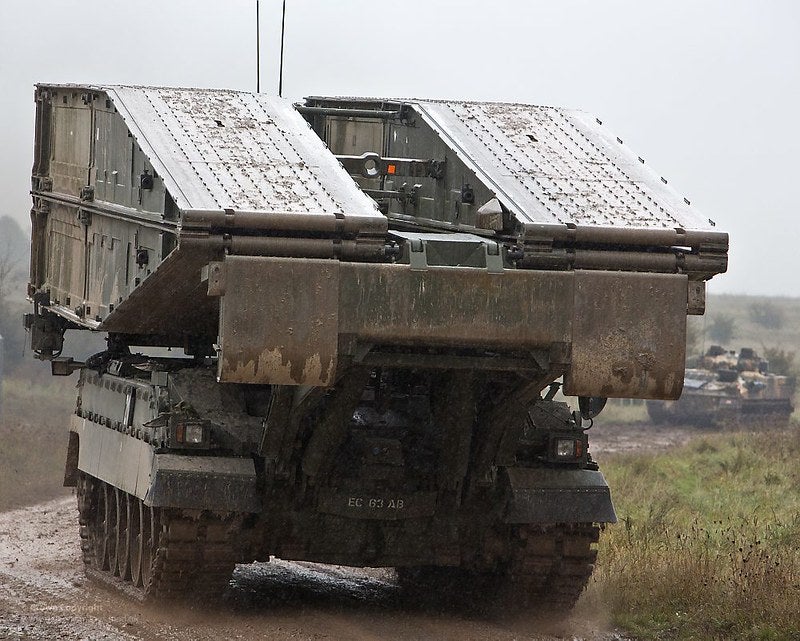
Babcock International Group has produced the first 3D printed printed parts for installation on the British Army’s in-service armoured fleets.
It is the first time a UK Ministry of Defence (MoD) supplier has used 3D metal printed parts to repair and extend the life of the armed force’s armoured vehicles.
The aim of additively manufactured parts is to address the increasing technical and commercial obsolescence challenges.
The development represents a key milestone for the company’s longer-term global advanced manufacturing investment programme.
Babcock chief technology officer Dr Richard Drake said: “This marks a major milestone in finding solutions for obsolete parts and in tackling resilience in the supply chain, some of the biggest challenges engineering and manufacturing businesses like ours are facing. We’re using disruptive technologies to address that.
“For us, this is part of a growing investment programme around advanced and additive manufacturing, which we can now progress to other areas of our business and that is hugely exciting for Babcock.”
The company noted that the steel components have been fitted onto in-service Titan and Trojan vehicle fleets.
Specifically, the 3D metal printed parts have been used on the vehicles’ periscope system.
According to Babcock, the Additive Layer Manufacturing process will allow the company to print parts that are obsolete in just days, whenever and wherever it is required.
HQ Field Army assistant chief of staff for equipment brigadier Phil Prosser said: “Additive has disrupted industry manufacturing processes and created an agile alternative to traditional mass manufacture.
“This ability to rapidly manufacture parts will allow our equipment to rapidly deploy on operations, and to stay in the fight for longer. This is battle winning activity and we are committed to this collaboration and will continue to learn at this impressive pace.”
In partnership with Plymouth Science Park (PSP), Babcock opened a new Additive Manufacturing centre in February 2022.
Last year, the company reached an agreement with IAI and ELTA Systems to support the MoD’s SERPENS programme.