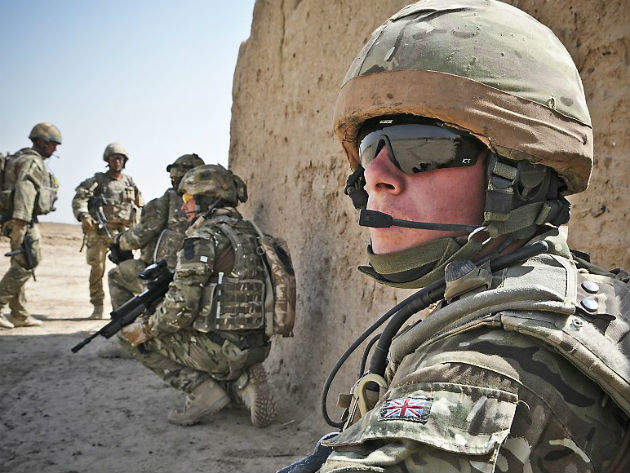
British troops fighting on the frontline are issued with advanced body armour to protect them against ballistic threats on the battlefield. Two main types of body armour are used by UK forces: the Osprey assault body armour kit, and the newer Virtus system that is currently being rolled out.
Throughout Operation Herrick, a lot of work was done to improve ergonomics, reduce weight and increase protection levels to keep personnel safe. One of the technologies that has had a significant impact on body armour is the increased move toward the use of ceramic plates, particularly as militaries looked to up protection levels while keeping the weight burden on the wearer as low as possible.
The problem with ceramic components is that they are extremely brittle, so while they are highly effective at stopping impact from bullet and shrapnel strikes, if they are dropped or shocked during the day-to-day rough and tumble of the battlefield, fractures can form within the ceramic that are very hard – if not impossible – to see with the naked eye.
Taking up the challenge
This challenge was taken up by Plextek under a research project run by the UK’s Centre for Defence Enterprise (CDE). In 2014, the CDE ran a challenge looking for future armour concepts, as a way for the Defence Science and Technology Laboratory and the wider UK Ministry of Defence (MoD) to identify novel technologies being developed by industry. The project looked to readdress the balance of short-term improvements in armour technology throughout Operation Herrick by taking a more forward-looking stance and considering how new technologies could be utilised to keep troops better protected on the future battlefield.
“The fractures that can form within the ceramic component of armour are very difficult to spot just by looking at the surface of the plate, as the fractures can be hairline,” explains Plextek technology lead for defence and security Aled Catherall. “Just like having a crack in your car’s windshield, the problem is that over time those fractures can grow and potentially impair the armour’s ability to do what it is intended to do.”
During Operation Herrick body armour had a significant logistics footprint in order to tackle this issue. At the end of every six-nine month tour of duty an entire tour’s worth of body armour – around 9,000 plates – were sent back to the UK for individual x-rays. In addition to being an expensive and lengthy process taking around three months, it also meant that the MoD had to procure double stocks of armour so that the incoming tour had enough armour to use while the last batch was being checked.
“We identified a requirement for a solution that would allow soldiers to quickly and easily determine the integrity of their body armour in the field,” Catherall says. “So we put forward a proposal under the CDE competition for a ‘push to test’ concept that could indicate to the soldier whether or not the armour has a fracture as part of their routine equipment checks.”
Not only would such a solution provide a cost-saving, as only those plates that were flagged as having a fracture would require returning to the UK for an X-ray,but it would also ensure that each soldier knows the integrity of their armour at all times.
Monitoring armour integrity
The result is the armour integrity monitoring device – a small sensor that monitors the vibrations within the ceramic components of the armour that detects the signature of the shockwave that is associated with the formation of a crack. In order to keep the weight as low as possible, the device is only slightly bigger than an AA battery.
The device sits on the side of the armour and can be retrofitted to the armour systems currently in use. The soldier pushes a button and the device shows a green light or red light, depending on whether a fault within the panel has been detected. At that point only the plates with a fault detected need to be returned to the UK for an X-ray.
The device was developed under the CDE project at a technology readiness level of 3/4, and a second round of funding within the last twelve months from Small Business Research Initiative (SBRI) took it to TRL 5/6 and saw a concept demonstrator developed.
“The SBRI funding allowed us to show that we can produce the effect in a small size/weight/power package device in real time – from our testing it has the potential to reduce the X-ray requirement by 96%,” Catherall says. “We conducted a live demonstration for key MoD stakeholders in June, and got very positive feedback on the cost-savings that this could provide in terms of the assurance that a soldier is going out as best protected as they can be.”
Plextek is working with Morgan Advanced Materials (a major supplier of armour to the UK MoD) to take the device to market in the summer 2017 timeframe, and is currently working on a production standard prototype that will be marketed to the MoD and international customers.
Further down the line the company is looking to address the issue of military vehicle armour integrity following ballistic and mine strikes using a device based on the same technology. A condition monitoring device that provides hostile fire indication could be used to show up small fractures in areas of the vehicle that aren’t easily visible.