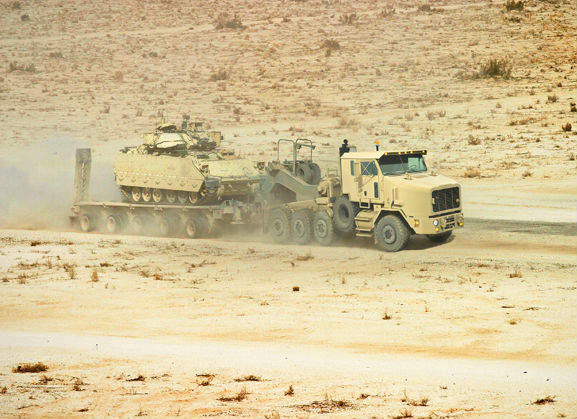
TerraMax integrates high-power military computers, intelligence, drive-by-wire technology and advanced distributed sensing systems to allow unmanned ground vehicles (UGVs) to run with no driver and limited supervision. The technology comes in a kit that can be applied to military vehicles while retaining the vehicle’s original utility, crew comfort levels and payload capacity.
The system’s development has involved a number of branches of US military research offices, with the technology evolving through various iterations and variants to meet the needs of projects and programmes set on increasing the autonomous capabilities of ground vehicles for land forces. Each step of the process has enriched TerraMax to the point where it is now ready to deliver force protection and multiplication advantages for multiple mission profiles.
The wayback machine
The first effort to develop the technology that grew into TerraMax was spun out of the Defense Advanced Research Projects Agency (Darpa) Grand Challenge of 2004. The driverless car competition sought technology that was capable of performing as a logistics vehicle, travelling from point A to B in a desert environment – similar to what was going on in Iraq at the time.
Oshkosh teamed with partners including Rockwell Collins, Ohio State University and a number of other vision and automotive companies for the competition, entering a system based around an Oshkosh vehicle. Although none of the competitors’ robot vehicles finished the specified route, the effort – along with the 2005 Grand Challenge the following year – spurred innovation among industry and academic universities to get the technology off the ground.
“The motivation at the time was force protection, with the idea being that if you take the people out of the cabs of these vehicles and it gets blown up by an IED no one gets hurt or killed,” says Oshkosh Advanced Products Group chief engineer of unmanned systems John Beck. “Darpa was very motivated because while there were a lot of things going on in the robotic field at that time nobody was really making any strong headway, so they thought that by standing up this competition they would entice innovation.”
Building capability
Oshkosh took on more development work with the team for the 2005 challenge, but it was the Darpa Urban Challenge of 2007 that took the technology to the next stage.
While the Grand Challenges required the ability for vehicles to drive autonomously in austere conditions and navigate in GPS-denied areas, the Urban Challenge brought dynamic obstacles into play including: the ability for the vehicle to follow the road rules, wait to cross intersections, and to drive and merge safely among other moving vehicles. The Oshkosh team reached the finals of the competition with its entry.
“At that point Darpa was satisfied that with the right amount of funding and innovation things could happen quite quickly, and then we started working with the US Navy and Marine Corps under a contract with the Naval Surface Warfare Centre in Panama City,” Beck says. “They were developing a counter-IED device and wanted an autonomous truck that could streamline their testing processes, and they also wanted to assess our technology for cargo-carrying missions.”
Working with the navy provided important feedback for the Oshkosh team, and helped bring the technology closer in line with what military forces were looking for. While the Darpa challenges had been based on the idea that any human interaction was a failure, what the navy was actually looking for was human-in-the-loop (HITL) interaction so that the truck could drive itself and then prompt the operator to take action when an impasse was reached. It also prompted Oshkosh to put further development into its interface technology to take it away from a complex engineering interface to something that could be handed to a young marine for operation with minimal training.
Widening the mission spectrum
Following the 2009 US Army Robotics Rodeo, Oshkosh was contracted by the Marine Corps Warfighter Laboratory for a project called Cargo UGV. The aim of the project was to develop and demonstrate the autonomous operation of a truck that could operate to the same specifications as the military’s Medium Tactical Vehicle Replacement (MTVR) vehicle for convoy operations in a mixed manned/unmanned fleet.
“At this point they weren’t testing the technical capabilities of the technology so much as trying to understand how these unmanned systems would impact their technologies, techniques and procedures, their standard doctrine and CONOPS [concept of operations],” Beck says. “So, what happens if these vehicles are unmanned and get blown up by an IED, or come under small arms fire, or even just get a flat tire? It was hugely beneficial.”
The Office of Naval Research picked up the research in 2014 and turned the focus from convoy operations to route clearance operations. This consisted of taking the autonomously-enabled MTVRs and applying different forms of IED detect and defeat technologies in a system-of-systems integration to demonstrate the capabilities that unmanned vehicles could bring to the route clearance mission. Key here was TerraMax’s open architecture design that enables third-party sensors and equipment to be easily integrated via an open standards interface.
Applying innovation
Today, TerraMax includes an impressive array of technologies to enable capability across a wide mission spectrum. Command Zone computer-controlled, multiplexed electronics technology operates and diagnoses all by-wire vehicle systems, with the multi-modal sensor suite consisting of LIDAR, radar, vision and military grade Global Navigation Satellite System (GNSS). The Operator Control Unit (OCU) allows operators to create and load route information and manage internal operations and autonomous systems status, while operability is possible in manned, tele-op, leader-follower and full autonomy profiles.
Oshkosh is currently positioning TerraMax for both convoy and route clearance missions.
“There are advantages to both applications, and they are twofold: force protection and force multiplication,” Beck says. “For convoy a single operator can manage the operation of multiple unmanned assets, and if you take the MTVR which usually has three occupants – driver, driver assist and gunner – and allow them to do something else with a single person operating five trucks from a standoff distance of up to 1km line of sight, it makes a lot of sense.
“For route clearance, it’s more about force protection, because the current vehicles use sensors or a mine roller to detect and defeat mines, and the standoff distance is only as far away as the sensor or roller is from the occupant of the vehicle – so to be able to manage the operation of that vehicle from a distance of 500m away gives you a much greater standoff distance from the threat.”
The future
When it comes to what TerraMax could ultimately be capable of as potential customers refine their requirements, the possibilities are vast thanks to the work carried out to date.
“Right now TerraMax is not a production kit or solution, it’s a range of one-off high performing proof of concept prototypes, and because of the open-architecture approach we’ve taken, new capabilities to suit various mission or user sets can be easily integrated,” Beck says. “We’re seeing strong interest on the Department of Defense side, with some programmes in the works and draft documents out there, and the idea is that over time as these become programmes of record or we approach a production-ready solution the cost will come way down and vehicles will either be supplied ready for this technology, or enabled with the technology.
“The demand could go in one of three main directions, either a driver-assist direction to bring a safety component to manned vehicles, a leader-follower capability where unmanned vehicles follow in the tyre tracks of a manned lead vehicle, or then there’s a more futuristic possibility for supervised autonomous vehicles that are truly unmanned and making a lot more decisions and taking intelligent actions.”