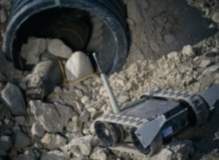
The job description for an explosive ordnance disposal (EOD) robot is fairly simple – disable or safely detonate a charge while the operator remains at a safe distance. Since the first Wheelbarrow robot – whose descendants are still serving today – took on its explosive opponent in 1972, engineers and researchers have constantly updated bomb disposal robots to meet the ever-changing challenge.
The latest bomb disposal robot programmes demonstrate the exceptional level of versatility, dexterity and diversity offered by new platforms to support EOD technicians in achieving their goals more safely and efficiently than ever.
CUTLASS delivers cutting edge bomb disposal
Northrop Grumman, which has kept the Wheelbarrow current right into the 21st century, rolled out a new design for the British Armed Forces in September 2012 through its Remotec UK business. Known as CUTLASS, it is a fast, manoeuvrable wheeled robot designed to assess a threat and deal with it in a single mission.
"CUTLASS can replace two traditional robots because it carries much of the capability on board," explains Danny Milligan, managing director of Northrop Grumman’s Information Systems Europe business. "It can go down to an incident, lay eyes on it and select appropriate tools to deal with whatever it finds."
By contrast, traditional EOD disposal often requires one robot to capture the situation on camera and another sent out with the tools to deal with it; otherwise a single robot returns to the operator having captured information about the explosive device to be kitted out appropriately. CUTLASS has on-board sensors and cameras which the operator uses to assess which items from the extensive on-board toolkit to select and use on the move. The operator uses a command and control unit with camera feed from CUTLASS to operate the robot from a distance; for instance from the back of a vehicle.
"Traditional robots require operators to physically watch the robot as it is deployed," says Milligan. "With CUTLASS you can operate it at range and blind."
Manoeuvring such an advanced robot doesn’t come easily, however. To get full value from the dexterity offered by the mechanical arm, which has several ranges of movement, takes a significant investment in training. However, the international version has been significantly simplified with more latitude over the control system.
"We’ve demonstrated an operator effectively controlling the robot using an eyepiece, and essentially an iPad and a joystick," adds Milligan.
CUTLASS continues to evolve to meet new challenges. Most recently, Northrop Grumman has developed a novel attachment for it designed to counter a specific threat related to a recent trend in the positioning of explosive ordnance, although no details can be revealed at the moment.
Security and defence exhibition attendees may have already encountered Northrop Grumman’s most nimble product to date, Lobster, which boasts twin manipulators so dextrous they can retrieve objects from the pockets of prone individuals. While most of Northrop Grumman’s research and development is done in-house, Lobster is a prime example of collaborative work.
"We had Lobster funded with Applied Minds, a Los Angeles-based organisation that Northrop Grumman has a long-standing association with. Some of their research was carried out on our behalf," says Milligan.
iRobot – a robot for every EOD mission
While CUTLASS was developed specifically to meet specific British military requirements, iRobot prides itself on offering a wide range of unmanned EOD solutions for all missions.
Mark Belanger, iRobot director of robotic products, explains: "Our smallest product, FirstLook, is a 5lb robot that fits in a backpack for dismounted EOD operations, all the way up to out 710 Warrior, a 500lb robot suitable for dealing with vehicle-borne IEDs, infrastructure missions or larger ordnance."
But iRobot’s most popular robot by far is the 60lb PackBot, which has been fielded since 2001 and undergone continual improvements to address evolving threats based on customer feedback since.
"It’s such a multi-faceted robot," says Belanger. "It has a three-ring manipulator arm making it capable of a wide range of things you can’t do with other robots. You can get into confined spaces, it can be integrated with various CBRN sensors, and it can drive down the aisle of an aeroplane and reach into overhead compartments."
Its versatility made it massively popular with US and international coalition forces in Iraq and Afghanistan, and its popularity has rubbed off on the law enforcement community in the US in post-war settings. Of 6,000 PackBots shipped, almost 4,500 are with US Armed Forces, and the remainder are spread across 35 partner nations, including the UK and countries in the Middle East region and Asia Pacific.
Can cash-strapped Western militaries use this commercial innovation for their own ends?
"Being deployed worldwide, it’s exposed to different kinds of environment from the desert sand environment in which it was mostly used in Iraq and Afghanistan," says Belanger. "It deals with the high heat and humidity and different environments in the Pacific, continues to deal with high temperatures and sand in the Middle East, and the diverse climates you have in Europe."
The way in which iRobot’s EOD robots are controlled varies with the size and application of the platform. The larger PackBot and 710 use a laptop-based controller, while the FirstLook uses an intuitive lightweight 2lb hand controller with an integrated screen and does not require training.
"For our 30lb 310 SUGV, of which we’ve shipped well over 1,000, we integrated an Xbox controller with a heads-up display," explains Belanger. "We wanted to give our customers and controller that was intuitive, easy to use and had a look and feel of something they may be familiar with in civilian life."
In terms of where the technology is heading, Belanger says the transition from Iraq to Afghanistan drove a push for smaller, lighter robots that supported modularity for dismounted missions in areas with limited infrastructure. FirstLook, for example, was originally designed as a reconnaissance robot, and the EOD community requested lightweight manipulator arms and a thermal camera for it to deal with explosive threats. Now there is a need post-Afghanistan for a larger robot class to deal with vehicle-borne IEDs and other threats that you may encounter in an urban scenario.
"In Iraq and Afghanistan, the army did a lot of blow-in-place to get rid of an IED threat," explains Belanger. "That’s not something you can do readily among a civilian population in an urban area; you need a robot that can isolate the threat and neutralise it without blowing up the neighbourhood."
PackBot is also being updated for applications beyond EOD, and iRobot has recently worked on integrating chemical, biological, radiological and nuclear (CBRN) sensors onto it.
"One of our research areas is giving our robots more versatility, so if they’re deployed by an EOD team they can work with CBRN and other sensors so they can be used for more than bomb disposal," concludes Belanger.
Robo Sally – dextrous limbs inspired by prosthetics
While much of Northrop Grumman and iRobot’s research is carried out in-house, they do occasionally work alongside academic and research institutions. But sometimes advanced technology developed through academic work attracts the eye of the military. Highly dextrous prosthetic limbs developed for amputees by the Applied Physics Laboratory (APL) at John Hopkins University in Baltimore, Maryland, have evolved into an EOD technology demonstrator fondly known as Robo Sally.
Michael McLoughlin, APL’s chief engineer for research and exploratory development, says: "We got involved in developing highly dextrous robotic limbs that could mimic everything a human limb could do via the DARPA funded Revolutionising Prosthetics (RP) programme. After developing the prosthetic limb, we started thinking about what else could we potentially utilise these limbs for. EOD robotics was an obvious application because many of the soldiers we worked with through the prosthetics programme had experiences amputations due to explosive devices."
APL asked the military robotics community what they wanted from the programme and found that as there would be multiple collaborators, and open architecture approach was essential. That led the researchers to the US Navy’s Advanced EOD Robotic System (AEODRS) programme and on to develop Robo Sally, a tracked humanoid torso equipped with the RP prosthetic limbs designed to demonstrate highly dextrous limbs in an EOD robot.
The RP limbs were designed to be operated by an amputee or person with a spinal cord injury by thought alone. For EOD operatives, APL developed a teleoperation solution that uses motion capture and gloves equipped with sensors than enable Robot Sally’s arms to mimic the operator’s actions.
"We also use a combination of computer vision and what we call semi-autonomous control to help reduce the burden on the operator," explains McLoughlin. "If the operator wants to grasp an object, you can identify an object and then the arm, using its own internal capability and embedded sensors, can do the final motions to grasp and hold an object, maintaining the correct pressure so it doesn’t slip."
While traditional EOD robots have a single degree of freedom and a simple pincer that can be opened, closed and rotated at the wrist, Robo Sally has five fingers which can be controlled independently. The wrist has three degrees of freedom, so as well as rotation it offers flex and extend deviation of the wrist, much like a human wrist, offering capability beyond any current fielded EOD robotics platform.
APL continues to work on the open architecture AEODRS programme focussed on the integration of advanced manipulators based on the RP limbs into a more rugged, less humanoid platform.
"For EOD applications generally you want things that are more rugged and able to lift heavier weights; you’re not as sensitive to the weight of the arm as you are with a human patient," says McLoughlin. "I think you’re going to see the same functionality, but the form factor will be different from Robo Sally as it’s adapted to the military environment."
Follow Berenice Baker on Google+