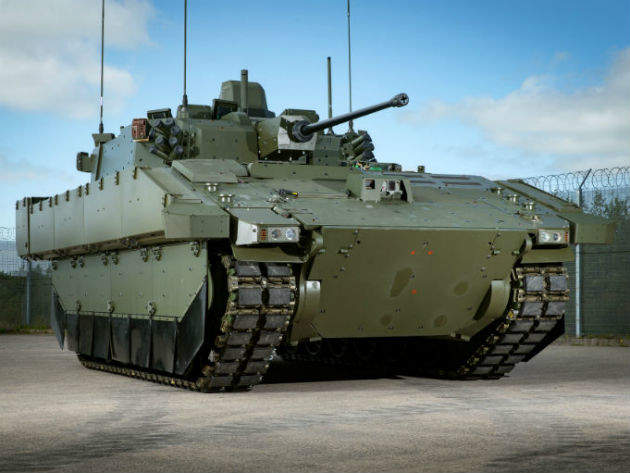
Tackling the heavy armour challenge to keep vehicles well-protected but light and agile is seeing development move in a number of directions. Alternatives to all-metal armour have been around for some time, but solutions have been largely limited to a handful of heavy vehicles such as Challenger 2 tanks and the US Army’s Stryker Armoured Combat Vehicle.
Now, backed by government investment and customer requirements at the highest level, the technology is being rolled out for vehicles of all sizes and roles, for both protective armour and vehicle components.
Ajax
In June it was announced that composite materials will form a key element of the ballistic armour protection system for the British Army’s in-development Ajax vehicle. The materials are being delivered to vehicle manufacturer General Dynamics by Permali Gloucester under a £15m contract.
Permali has worked on UK Ministry of Defence (MoD) projects in the past, including supplying an applique armour solution for the army’s Warthog platform; a composite roof for the Panther Command and Liaison vehicle; applique armour for the Oshkosh Heavy Equipment Transporter and Wheeled Tanker; composite moulding for blast protection for the Land Rover Revised Weapons Mounted Installation Kit (RWMIK); and blast protection panels and side skirts on the Wedgewood Counter Improvised Explosive Device Disposal (CIEDD) vehicle.
The company’s ballistic panels are manufactured using glass, aramid or ultra-high-molecular-weight polyethylene (UHMWPE) materials and thermoset resin systems or advanced thermoplastic matrices. These can include ceramic tiles for protection against armour piercing rounds, and aluminium or steel skins for greater rigidity and increased protection levels.
Ceramics
Ceramics are a type of composite armour that entered mainstream usage around 50 years ago when the material was developed for use on the British Army’s heavy vehicles. Known as Chobham armour, the success of this design led to it being used on M1 Abrams, Challenger 1 and Challenger 2 vehicles.
The advantage of ceramic armour is the material’s extreme hardness at a very light weight. Depending on the material’s properties, it also offers high strength, chemical resistance, corrosion resistance, wear and heat resistance and thermal expansion, insulation and conductivity.
The make-up and property combinations of ceramic armour varies from manufacturer to manufacturer, with many companies working in this space. Each material has a unique mechanical, thermal, biochemical and electrical properties, which can then be further altered and developed to suit specific applications.
Technology innovation
CeramTec, the supplier of advanced technical ceramics, works with four groups of ceramic materials: silicate ceramics (natural materials in conjunction with alumina); oxide ceramics (primarily metal oxides); non-oxide ceramics (based on carbon, nitrogen and silicon compounds); and piezo-ceramics (a group of materials used to convert mechanical parameters into electrical parameters or electrical signals into mechanical movement or vibration).
The company’s ceramics have been supplied as critical components in systems that offer ballistic protection for land vehicles, and it is one of the first to work in the area of transparent ceramics, with a system called Perlucor. The material weighs 30% less than conventional bullet-proof glass systems.
This ceramic can withstand extreme conditions and can be applied as transparent ballistic vehicle protection. As with typical ceramic armour, Perlucor comes in a standard 90x90mm tile that can be shaped with individual contours based on customer requirements. It can also be tailored to a specific thickness, generally between 2-10mm. The gluing technology used means that joints and edges are ‘invisible’, making it possible for an optical surface to be manufactured to produce large windows.
Hybrid
Ceramic hybrids – including metal-ceramic and metal-ceramic-composite hybrids – are also an option for providing increased protection by combining ceramics with materials that offer improved performance, such as increased strength. These hybrids delay ceramic failure in the event of a strike and help reduce spalling. The US Army’s Stryker vehicle has been fitted with the composite Modular Expandable Armor System (MEXAS, as have armoured vehicles in the German, Canadian, Swedish and Austrian armed forces.
CPS Technologies – a leader in developing and manufacturing advanced materials solutions and products – also works in this type of armour. The company’s HybridTech Armor tiles are ceramic tiles, reinforced with metal and metal matrix composites, which are then packaged in a hermetic layer of high-pressure cast aluminium. CPS believes this approach results in more consistent ballistic performance near tile edges, and makes assembly easier as the modules are tough enough to drill and bolt like metal, eliminating the needs for steel inserts at attachment points.
Components
The use of composite materials to reduce weight is beginning to move beyond armour to infiltrate every aspect of defence equipment, as manufacturers look to address customers’ transportability and manoeuvrability requirements. In June, FN Herstal introduced a newly developed carbon connection plate prototype for pintle weapon systems. By using composite materials, the company has reduced the weight of the connection plate (the plate that interfaces the carrier hard points with the weapon system) by 30%, while maintaining all of the structural properties of earlier versions.
Tencate provides lightweight 3D components for military vehicles for areas such as hatches, doors and bonnets, where weight is an obstacle to mobility. The company supplies composite solutions with ceramics to counter specific threats on the battlefield, as well as fibre-based solutions to provide protection against small calibre ammunition.
Sovereign capability
The development and manufacture of ceramic composite armour is increasingly backed at the government level in order to cultivate and protect sovereign capabilities.
The UK MoD’s Defence and Science Technology Laboratory (DSTL) is working on UK Plc capabilities in this sector with Kennametal Manufacturing UK. In 2013 a new spark plasma sintering (SPS) facility opened at Kennametal’s Newport facility, where specialised manufacturing capabilities for full size ceramic armour components for vehicles and body armour are being developed.
With an in-country ability to manufacture these components, the hope is that the UK will no longer be reliant on buying materials from foreign countries.
The future
Looking beyond lightweight armour, the US military is looking to rethink its entire approach to armour in future vehicles to enhance mobility and agility, with a focus on avoiding being hit with projectiles rather than simply being able to survive them.
This idea is being developed as part of the Defense Advanced Research Projects Agency’s (DARPA’s) Ground X-Vehicle Technology (GXV-T) programme. The programme recognises that today’s ground-based armoured fighting vehicles are better protected than ever, but face a constantly evolving threat as weapons become increasingly effective at piercing armour. While adding more armour has provided incremental increases in protection, it has also impeded vehicle speed and mobility and ballooned development and deployment costs.
The effort could see future vehicles designed around the concept of survivability through agility rather than solely protection: to autonomously avoid incoming threats via technologies that enable, for example, agile motion and active repositioning of armour.
Often considered to be a one-size-fits-all component of armoured vehicle development, armour technology is, on the contrary, a constantly evolving technology. The current objective is to go lighter while retaining strength; beyond that, the sky is the limit.