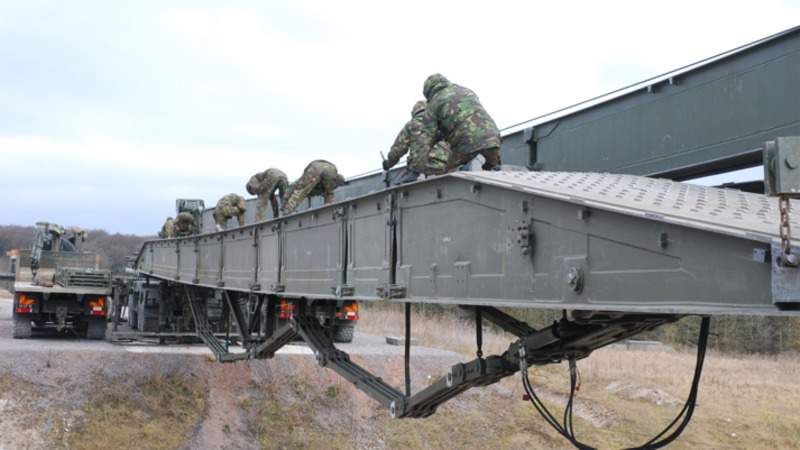
BAE Systems has successfully demonstrated the safety and performance of its new Modular Bridging System, supporting its bid to provide the system for the British Army and export customers.
During testing, the company simulated more than 22,000 crossings of the Challenger 2 Main Battle Tank on the system. These have the equivalent weight of 121,000 double-decker buses.
The simulation was carried out at the company’s bridge test facility in Telford, England.
Designed to offer a flexible and rapidly deployable military gap crossing solution, the new lightweight Modular Bridging System can be easily transported by air.
It can be used by army personnel to carry out assault crossings, restore vital lifelines and military routes, and provide rapid replacement of civilian infrastructure in combat and disaster relief.
The company has also completed environmental tests to demonstrate that the bridge would remain robust and effective throughout its entire operational life, including the adverse conditions that are expected in military use.
Several smaller tests were also conducted with more than 300,000 fatigue cycles being carried out on individual components.
BAE Systems bridging business manager John Lees said: “This project has been as much about improving techniques in manufacturing and performance as it has about testing bridges.
“We’ve carried out tests across even the smallest bridge components to allow us to confidently underwrite the performance of our bridges, and offer an innovative and cost-effective system that exceeds soldiers’ needs to 2040 and beyond.”
The bridge panels have been equipped with new Bluetooth-enabled sensors that help analyse approximately 100 strain readings each second.
This provides the soldiers with a more complete and real-time picture of the health of the bridge systems.
The development of the bridge involved 28,000 engineering hours.