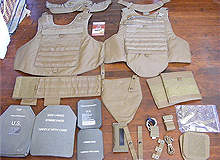
Modern military body armour for example consists mostly of fabrics, commonly with armour plates inserted as additional reinforcement. While this combination is able to protect the bearer even from attacks with 7.62mmx51mm Nato-calibre ammunition fired by rifles, fabrics are now being used that have the power to stop 9mm projectiles fired from handguns on their own.
The central tasks of ballistic protection are the absorption and the dissipation of energy caused by a ballistic impact. For this reason, bulletproof vests generally consist of a number of layers. Their fabrics or composite lay ups are made of yarns of high-performance fibres. At the impact of a bullet the material absorbs the kinetic energy – a handgun projectile travels at a speed of 400m a second – by stretching of fibres and other stiff fibres which disperse the load over a large area throughout the material. This slows the bullet down and finally hinders it from penetrating the body.
Rigid vs flexible conundrum
Body armour designed specifically to defeat rifle fire has to be more rigid, because those projectiles travel at speeds of around 800m a second. Therefore, besides the layers with fibres, hard materials such as ceramics or metal plates have to be inserted. The protective plates absorb and dissipate this greater kinetic energy upon impact and also the bullet itself gets blunted. According to experts from the German military’s Research Institute for Materials, Fuels and Lubricants (WIWeB) “For military use you always need this combination of fibres and hard inserts as each material alone would not stand a chance,”
The two most critical factors for high performance fibres are therefore their strength and how much they can extend before fraction. During the last few decades, different chemical materials have been invented and constantly upgraded to achieve better effects. Today’s main high-performance fibres, Kevlar, Twaron, Dyneema and Spectra are based on the chemical bonds of para-aramid and high performance polyethylene.
“Today’s high performance fibres mainly used for military purposes are Kevlar and Twaron, but in the future high performance polyethylene will become more important,” according to the German Institute.
The German military, for example, uses protective vests made of para-aramid fibres Twaron or Kevlar in combination with ceramic inserts.
Stopping power
Kevlar is the trademark for aramid fibres, produced by US company DuPont. Its Kelvar KM2 technology is used in different armour applications, including the Interceptor body armour used by the US military. Kevlar has an equal weight basis to steel but is five times stronger, while being more flexible. The latest-development Kevlar XP reduces potentially serious ballistic and trauma injuries due to its new structure. At the moment the company is researching a completely new high-performance fibre named M5, which is supposed to incorporate ultra-high strength as well as ultra-high thermal and flame resistance.
Twaron is a very strong, light para-aramid fibre developed and produced by Dutch company Teijin Aramid. According to the company, weight can be reduced between 30% and 60% compared to ballistic steel by incorporating Twaron into vehicle armour. Its laminated fabric technology (LFT) SB1 is a very flexible and thin laminate comprising two fabric layers sandwiched with three layers of ultra-thin PE film, which special construction hinders intruding bullets to push the yarns apart. The latest development Twaron LFT SB1 plus decreases the back face deformation with about 30%, without compromising the wear comfort.
Dyneema is a high-performance polyethylene fibre produced by DSM Dyneema, which is part of Dutch company Royal DSM.
According to its manufacturer, which calls it the world’s strongest fibre, it is 15 times stronger than steel and 40% stronger than aramid on a equal weight basis and the only stand-alone composite in the world that protects against bullets fired by Russian AK-47 assault rifles. Two of its latest developments are the unidirectional composite Dyneema HB80, which has been developed to increase fragmentation performance while reducing the weight of combat helmets, and the ballistic tape Dyneema BT10 for use in lightweight, high-protection vehicle armour.
Breaking point
A challenge for high-performance fibres is their sensitivity to environmental influences like high temperature, increased humidity or sweat. According to experts at the WIWeB this would accelerate their normal aging process and could make them vulnerable to degradation in the end. Therefore these special protective layers of body armour must be protected from those environmental influences to provide long-term durability.
Besides this, recent military scenarios put a constantly high demand on the performance of the fibres as they increasingly include multiple bullet strikes, stronger ammunition, IED or small shrapnel from explosives like hand grenades.
Future fibres
Aside from existing materials, carbon nanotubes are an ideal candidate material for future bullet-proof vests due to their unique combination of exceptionally high elastic modulus and high yield strain,” says Dr Yashwant Mahajan from the Center for Knowledge Management of Nanoscience and Technology at Secunderabad, India.
The Indian scientist says, that carbon nanotubes (hollow cylinders of carbon that are just one-atom thick) would possess a very high hardness: “When they are for example incorporated into a polymer matrix composite armour tile, they will likely deform, erode or fracture the projectile.” Due to their unique combination of high elastic modulus and high strain to failure, they would be capable of elastically storing an extreme amount of energy, Mahajan explains. These characteristics could cause the bullet to bounce off or be deflected, which would also provide improved protection against blunt trauma effects and at the same time improve multi-hit capability.
Such nanotube fibres also possess characteristics that enable them to be woven as a cloth, or incorporated into composite materials.
As woven or non-woven fabric neat or composite fibres carbon nanotubes could achieve exceptional ballistic performance, says Mahajan. Incorporated into current fibres they could improve their ballistic performance by improving stiffness, strength and toughness. These could, for instance, be incorporated into the polymer matrix composite, metal or ceramic inserts to enhance their hardness, toughness and erosion resistance.
“For instance, incorporated into the body armour, these nanotube-based neat or composite fibres have the potential to protect a person from the most aggressive ballistic threats of the future,” Mahajan predicts.