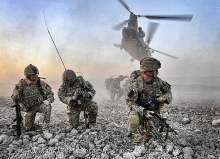
With modern ground operations constantly increasing in complexity and technological sophistication, today’s soldiers are expected to offer more than just boots on the ground. With communication equipment, advanced optics, GPS and video recording equipment now routinely used, today’s troops are increasingly viewed as all-in-one warfighting platforms.
All of this means a wider range of soldier-mounted electronics, and the batteries required to power them over long periods in tough conditions. This equipment adds up to a heavy burden for soldiers, whose packs can weigh up to 75kg – a nightmarish prospect when patrolling some of the world’s most sweltering combat zones.
With issues like weight, reliability and battery life high on the list of priorities for frontline soldiers, any advances that reduce the reliance on endless AA and AAA battery packs are in high demand. The development of a better power supply system would also be welcomed from a top-level cost perspective, as the reduction or elimination of the constant stream of spare batteries would bring significant savings.
BAE’s structural batteries: powering future soldiers
An innovative and highly promising new battery concept unveiled by BAE Systems last month could provide a viable alternative to the current battery conundrum being experienced by armed forces. Structural batteries, as BAE has dubbed them, bring the ability to build rechargeable battery power into the structure of electrical devices themselves, shedding excess weight of traditional batteries and removing the cost and logistical challenges involved in constantly supplying batteries to the frontline.
“Structural batteries can be used in virtually anything that requires electricity, from small gadgets to entire vehicles,” said BAE’s capability technology leader for materials Alex Parfitt. “They can not only support our soldiers on the frontline, but also revolutionise technology in the consumer market by allowing more efficient, elegant and lighter designs.”
The technology, which is still in the early stages of development, allows nickel-based battery chemistries to be embedded into composite materials like carbon fibre and glass-reinforced plastic. The structural batteries have been successfully incorporated as the power source in a micro unmanned aerial vehicle (UAV) as well as a simple torch, although a collaboration with the motorsport industry has proved to be the most powerful demonstration of the technology so far.
Structural batteries have been incorporated into the wing of the Lola-Drayson B12/69EV zero-emission 850 horsepower prototype racecar, intended to be the world’s fastest electric racing vehicle upon completion, to power elements of its on-board electronic systems.
The demonstration is not only intended to show the potential of structural batteries in a non-military context, but also to help speed up the development of military prototypes, as a BAE spokesman explained.
“The motorsport industry has quick turnaround times compared to defence, so our technology gets matured faster and gets real world experience on a vehicle,” he said. “By proving the technology in this area it could lead to the technology being accepted into the military domain.”
Overcoming design issues
However, at this early stage of BAE’s research into structural batteries, some questions remain. Although the reduction in weight could provide a fundamental improvement to the design of a host of military platforms, it will still be imperative that reliability and longevity of the power supply remains at least as good as the current battery regime.
In this respect, there may be some operational challenges to overcome. After all, structural batteries would have to work on a rechargeable system, which means soldiers would presumably be unable to easily replace their power supply while in the field. Also, if structural batteries are built into the exterior surfaces of devices, would that leave them more vulnerable to losing power in the case of damage or wear-and-tear?
BAE’s spokesman said the company has been working on ways to ensure solid performance and absolute reliability.
“Currently our research is still in low TRL [technology readiness level] development but we have reached 25 watt hours per kg, or just below a standard car battery in terms of energy density,” he explained.
“We use a nickel battery chemistry that will last decades rather than years like a lithium battery, so it would last for the lifetime of the platform.
“If our structural battery were to be damaged, it has the same tolerance as carbon composite so it can take some damage and still work. You can also make the batteries cellular, so if one or two cells are damaged the other cells still function and allow what the battery is powering to operate.”
Supporting future technology
The elimination of the weight associated with separate battery packs has ramifications which could affect almost all levels of the armed forces, from infantry to ground vehicles and even aircraft. “The main benefits are weight saving and cost saving,” said BAE’s spokesman.
“Soldiers could have lighter kit and more space to carry what they would really like to have with them in theatre. There is also a logistical burden in supplying replacement / spare batteries to the front line.
“If you look at future UAVs, a large amount of the weight is taken up by batteries that power the platform. By making parts of the structure, for example the wings, the battery, you reduce weight and allow the UAV to increase its payload, or it could be smaller and still deliver the same payload.”
Although BAE is not currently commenting on the specifics of what future technologies structural batteries could potentially support, the company’s spokesman notes that it is a technology that meshes well with renewable power sources. “The key to structural batteries is that they can be incorporated into almost any structure so solar panels could be used and not only be part of the structure but also the battery,” he said.
As the demand for renewable technologies to be incorporated into military hardware increases, structural batteries could be a key enabler in their deployment.
If solar batteries are incorporated into the exteriors of military vehicles or even the clothing of soldiers, then structural batteries could potentially be placed right alongside them to harness their gathered energy and form a single, self-sustaining power supply.
Given that wearable solar cells are being actively investigated by both the UK Ministry of Defence (MoD) and the Australian Defence Force (ADF), the possibility of these two technologies being merged in the next few years must be one that BAE is considering.
It’s still too early to get a definitive picture of how the structural battery will fit into the military power supply landscape. At this fragile point in the technology’s development, any number of technical or financial issues might scupper its eventual deployment. However, if the undeniable raw potential of structural batteries can be harnessed and refined to produce workable devices, which help to make a soldier’s job easier, this technology could help move military power supply and storage away from the AA and into the 21st century.