
Metal component manufacturer SPEE3D has announced that the Australian Army used its 3D metal printing technology in a two-week-long field exercise in the Northern Territory.
The army-deployed SPEE3D’s WarpSPEE3D 3D metal printer, which is capable of printing large metal parts up to 40kg at a speed of 100g/min.
The printer uses cold spray technology to enable faster metal part production compared with conventional processes.
WarpSPEE3D underwent first field trial in June.
SPEE3D CEO Byron Kennedy said: “This second field deployment proves our technology is a genuine solution for expeditionary metal 3D printing.
“This two-week trial demonstrates the WarpSPEE3D is a robust workhorse that is capable of printing real parts and solving real problems in the field.
How well do you really know your competitors?
Access the most comprehensive Company Profiles on the market, powered by GlobalData. Save hours of research. Gain competitive edge.
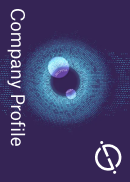
Thank you!
Your download email will arrive shortly
Not ready to buy yet? Download a free sample
We are confident about the unique quality of our Company Profiles. However, we want you to make the most beneficial decision for your business, so we offer a free sample that you can download by submitting the below form
By GlobalData“It also proves that soldiers can take control of the whole workflow of creating the spare parts they need, from design to printing and post-processing, right here where they need them.”
Notably, the Australian Army allocated A$1.5m to a SPEE3D technology pilot in February. The move included a 12-month trial period to evaluate the feasibility of deploying 3D metal printers on-base and in the field.
Subsequently, SPEE3D collaborated with the Advanced Manufacturing Alliance (AMA) and Charles Darwin University (CDU) to deliver the programme.
The use of 3D metal printing technology is aimed to expedite the availability of unique parts to the army.
With bases in Darwin and Melbourne, SPEE3D focuses on manufacturing metal additive manufacturing technology.