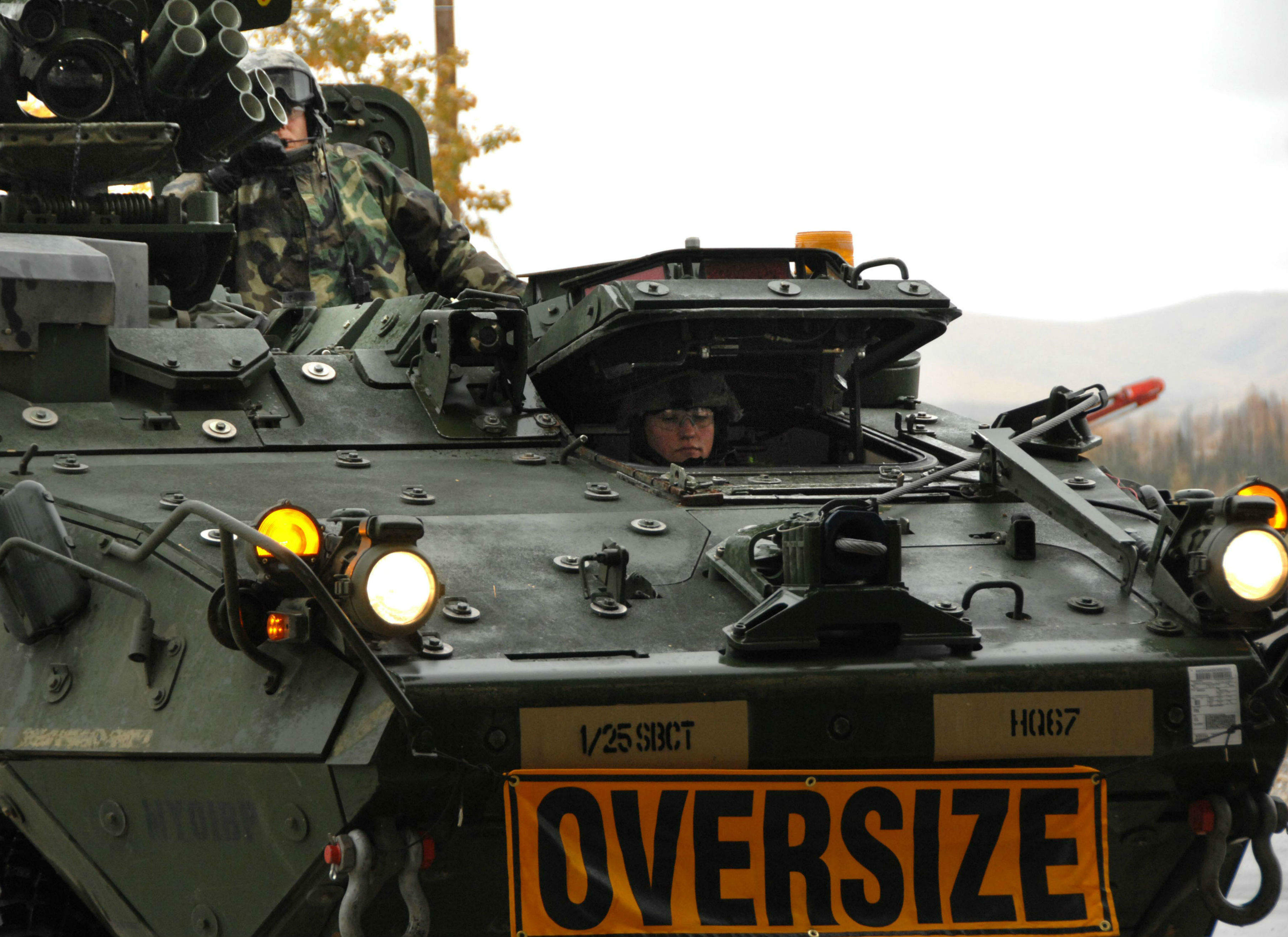
In September the US Defense Advanced Research Projects Agency (DARPA) awarded a $1.5m contract to QinetiQ to develop an electric drive hub for the agency’s Ground X-Vehicle Technologies (GXV-T) programme. QinetiQ’s work will focus on the development of hub drive technologies that improve the mobility and survivability of ground vehicles. Although the finer details of the work have not been released, QinetiQ has said that it will draw on its experience of developing electro-mechanical transmissions for tracked and wheeled vehicles to create a unit that can be contained within a 20" wheel rim. With this unit the company aims to improve mobility through "enhanced power, torque, integral braking and high efficiency", and improve the safety of thevehicle’s occupants by removing the drive shafts and gearboxes in order to reduce the amount of lethal shrapnel created in the event of an improvised explosive device (IED) detonation.
The hope is that the absence of the drive shaft and gearbox will combine better performance with a significant weight saving, which is critical for mobility. Furthermore, the design has the potential to "open up future design possibilities, such as fully independent suspension with significantly increased travel", according to the company, as well as an increased degree of architectural flexibility that could enable vehicles to be configured in new ways to offer even greater protection to occupants.
Back to the drawing board
DARPA’s GXV-T programme seeks to enact a shift away from the US military’s well-worn paradigm of "more armour equals more protection" for ground vehicles. Taking this route over the past decade has left ground vehicles over-burdened with armour – and heavier than ever before – which in turn left the soldiers that rely on them with a limited ability to rapidly deploy and manoeuvre in theatre. At the same time, the add-on armour model has rendered vehicles more expensive to design, develop, field and replace, and created complicated and enlarged logistics requirements once they are deployed.
Most critically, the weapons and munitions that all this armour is designed to defend against have been advancing at a faster rate than armour’s ability to withstand penetration, leaving military forces in a seemingly never-ending race against a quickly evolving and increasingly resourceful enemy.
Faced with this challenge, DARPA is going back to the drawing board with the GXV-T programme. Although still in its early stages, the programme is looking at technologies that can stay ahead of the adversaries with new means; rather than simply avoiding penetration with improved armour, it wants to avoid detection, engagement and, as a result, hits and penetration.
DARPA envisions tomorrow’s land vehicle as one with a 50% reduction in weight, 50% reduction in crew requirements, 100% increase in speed, and a reduced vehicle signature. The vehicle would also be able to manoeuvre in 95% of terrain.
In order to achieve this DARPA is setting its sights high, with contracts such as the one awarded to QinetiQ looking to improve mobility and survivability, and other areas of development set to include improved autonomous support for crew functions and enhancements in technologies to reduce vehicle infrared, acoustic and electromagnetic signatures.
GE’s ‘leap ahead’ technology
Another area of significant research and development for military ground vehicles is power architectures to improve size, weight and power attributes.
In December 2015, GE Aviation was awarded a contract by the US Army’s Tank Automotive Research, Development and Engineering Center (TARDEC) to support its next-generation vehicle electrical power architecture ‘leap ahead’ technology development. The contract will see GE demonstrate its silicon carbide (SiC) MOSFET technology as a potential alternative to current silicon-based systems that will allow for better management of the vehicle’s available on-board power to increase mission capability.
"Where next-gen ground vehicles are moving toward more-electric (hybrid) architectures, the traditional 28Vdc systems are being augmented or replaced by high voltage systems which can be 600Vdc or higher," says Rick Eddins, electrical power applications leader at GE Aviation. "More electrical power is a requirement for future vehicles to support new systems; and SiC improves all metrics related to power generation, conversion and distribution functions. These metrics include size, weight, power density and efficiency."
SiC comes into play here because of its higher operating junction temperature capability and higher frequency operation. GE’s SiC devices can operate at junction temperatures of +200ºC whereas traditional silicon devices can be reliably operated to +150ºC.
"A goal of TARDEC is to demonstrate high temperature electronics that can operate when cooled from the engine coolant loop, which operates at 105ºC – this capability would reduce the amount of active cooling the vehicle would need to include in its design, reducing vehicle weight and improving mobility," Eddins explains. "SiC devices are demonstrating that TARDEC’s goals are within sight: SiC’s higher frequency capability can be exploited though improved efficiency or improved power density. Size and weight reductions are typically 50% or better."
Under the contract the company will demonstrate the benefits of the SiC MOFSET in two systems: a 35kW main engine cooling fan controller and a 3kW coolant pump controller.
"GE’s SiC MOSFETs enable the power electronics to operate reliably in these high temperature environments," says Eddins.
"Integrating the electronics onto the fan/pump eliminate the individual motor drive line replaceable unit (LRU) which would typically be mounted elsewhere in the vehicle and require additional cables and cooling hoses."
Effectively, by integrating the SiC controller electronics onto the engine cooling fan, the need for a separate liquid-cooled motor drive line LRU is eliminated – along with related cooling hoses and interconnecting cables – simplifying vehicle installation and freeing up space and weight for other systems, effectively improving the vehicle’s available on-board power architecture.
According to Eddins, high-voltage architectures have been demonstrated in military ground vehicles using traditional silicon devices / power modules, and prototype vehicles have demonstrated SiC enabled power electronics.
Now, with several reliability programmes underway, GE is demonstrating that SiC is as robust as silicon and can be designed into those applications demanding the higher performance silicon carbide provides. And with most branches of the US military currently researching applications for SiC, it looks set to form an integral part of the next-generation vehicle fleet.